6-calowe przewodzące podłoże kompozytowe SiC 4H Średnica 150 mm Ra ≤ 0,2 nm Osnowa ≤ 35 μm
Parametry techniczne
Rzeczy | Produkcjastopień | Atrapastopień |
Średnica | 6-8 cali | 6-8 cali |
Grubość | 350/500±25,0 μm | 350/500±25,0 μm |
Polityp | 4H | 4H |
Oporność | 0,015-0,025 omów·cm | 0,015-0,025 omów·cm |
TTV | ≤5 μm | ≤20 μm |
Osnowa | ≤35 μm | ≤55 μm |
Chropowatość czołowa (Si-face) | Ra≤0,2 nm (5μm×5μm) | Ra≤0,2 nm (5μm×5μm) |
Główne cechy
1. Zaleta kosztowa: Nasze 6-calowe przewodzące podłoże kompozytowe SiC wykorzystuje opatentowaną technologię „graded buffer layer”, która optymalizuje skład materiału, obniżając koszty surowców o 38% przy jednoczesnym zachowaniu doskonałych parametrów elektrycznych. Rzeczywiste pomiary pokazują, że tranzystory MOSFET o napięciu 650 V wykorzystujące to podłoże osiągają 42% redukcję kosztów jednostkowych w porównaniu z rozwiązaniami konwencjonalnymi, co ma istotne znaczenie dla promowania stosowania urządzeń SiC w elektronice użytkowej.
2. Doskonałe właściwości przewodzące: Dzięki precyzyjnym procesom kontroli domieszkowania azotem, nasze 6-calowe przewodzące podłoże kompozytowe SiC osiąga ultraniską rezystywność na poziomie 0,012-0,022 Ω·cm, z kontrolą odchyleń w zakresie ±5%. Co istotne, utrzymujemy jednorodność rezystywności nawet w obrębie 5-milimetrowej krawędzi płytki, rozwiązując długotrwały problem efektu krawędziowego w branży.
3. Wydajność termiczna: Moduł 1200 V/50 A opracowany z wykorzystaniem naszego podłoża wykazuje wzrost temperatury złącza zaledwie o 45°C powyżej temperatury otoczenia przy pełnym obciążeniu – o 65°C mniej niż porównywalne urządzenia krzemowe. Jest to możliwe dzięki naszej kompozytowej strukturze „3D Thermal Channel”, która poprawia poprzeczne przewodnictwo cieplne do 380 W/m·K i pionowe przewodnictwo cieplne do 290 W/m·K.
4. Zgodność z procesem: Dla unikalnej struktury 6-calowych przewodzących podłoży kompozytowych SiC opracowaliśmy dopasowany proces cięcia laserowego stealth, który osiąga prędkość cięcia 200 mm/s, jednocześnie kontrolując odpryskiwanie krawędzi poniżej 0,3 μm. Dodatkowo oferujemy podłoża wstępnie niklowane, które umożliwiają bezpośrednie łączenie matryc, oszczędzając klientom dwa etapy procesu.
Główne zastosowania
Krytyczny sprzęt inteligentnej sieci:
W systemach przesyłu prądu stałego ultrawysokiego napięcia (UHVDC) pracujących z napięciem ±800 kV, tranzystory IGCT wykorzystujące nasze 6-calowe przewodzące podłoża kompozytowe SiC wykazują znaczną poprawę wydajności. Urządzenia te osiągają 55% redukcję strat przełączania podczas procesów komutacji, jednocześnie zwiększając ogólną sprawność systemu do ponad 99,2%. Doskonała przewodność cieplna tych podłoży (380 W/m·K) umożliwia projektowanie kompaktowych przekształtników, które zmniejszają powierzchnię stacji elektroenergetycznych o 25% w porównaniu z konwencjonalnymi rozwiązaniami opartymi na krzemie.
Nowe układy napędowe pojazdów energetycznych:
Układ napędowy wykorzystujący nasze 6-calowe przewodzące podłoża kompozytowe SiC osiąga niespotykaną gęstość mocy falownika wynoszącą 45 kW/l – o 60% więcej niż poprzednia konstrukcja oparta na krzemie o napięciu 400 V. Co najbardziej imponujące, układ utrzymuje sprawność na poziomie 98% w całym zakresie temperatur roboczych od -40°C do +175°C, rozwiązując problemy z wydajnością w niskich temperaturach, które nękały pojazdy elektryczne w północnych klimatach. Testy w warunkach rzeczywistych pokazują 7,5% wzrost zasięgu w zimie dla pojazdów wyposażonych w tę technologię.
Przemysłowe napędy o zmiennej częstotliwości:
Zastosowanie naszych podłoży w inteligentnych modułach mocy (IPM) do przemysłowych systemów serwo zmienia automatyzację produkcji. W centrach obróbczych CNC moduły te zapewniają o 40% szybszą reakcję silnika (skrócenie czasu przyspieszania z 50 ms do 30 ms) przy jednoczesnym obniżeniu poziomu szumu elektromagnetycznego o 15 dB do 65 dB(A).
Elektronika użytkowa:
Rewolucja w elektronice użytkowej trwa, a nasze podłoża umożliwiają stworzenie szybkich ładowarek GaN o mocy 65 W nowej generacji. Te kompaktowe zasilacze osiągają 30% redukcję objętości (do 45 cm³) przy jednoczesnym zachowaniu pełnej mocy wyjściowej, dzięki doskonałym właściwościom przełączania konstrukcji opartych na SiC. Termowizja pokazuje maksymalną temperaturę obudowy na poziomie zaledwie 68°C podczas ciągłej pracy – o 22°C niższą niż w przypadku konwencjonalnych rozwiązań – co znacznie wydłuża żywotność i poprawia bezpieczeństwo produktu.
Usługi dostosowywania XKH
XKH zapewnia kompleksowe wsparcie personalizacji podłoży kompozytowych SiC przewodzących o grubości 6 cali:
Dostosowywanie grubości: Opcje obejmujące specyfikacje 200 μm, 300 μm i 350 μm
2. Kontrola rezystywności: Regulowane stężenie domieszki typu n od 1×10¹⁸ do 5×10¹⁸ cm⁻³
3. Orientacja kryształu: obsługa wielu orientacji, w tym (0001) poza osią 4° lub 8°
4. Usługi testowe: kompletne raporty z testów parametrów na poziomie wafli
Nasz obecny czas realizacji od prototypu do produkcji masowej wynosi zaledwie 8 tygodni. Dla klientów strategicznych oferujemy dedykowane usługi rozwoju procesów, aby zapewnić idealne dopasowanie do wymagań urządzenia.
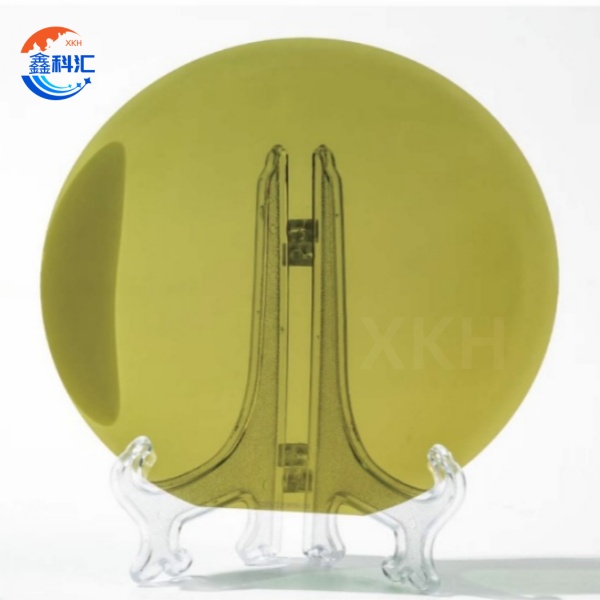
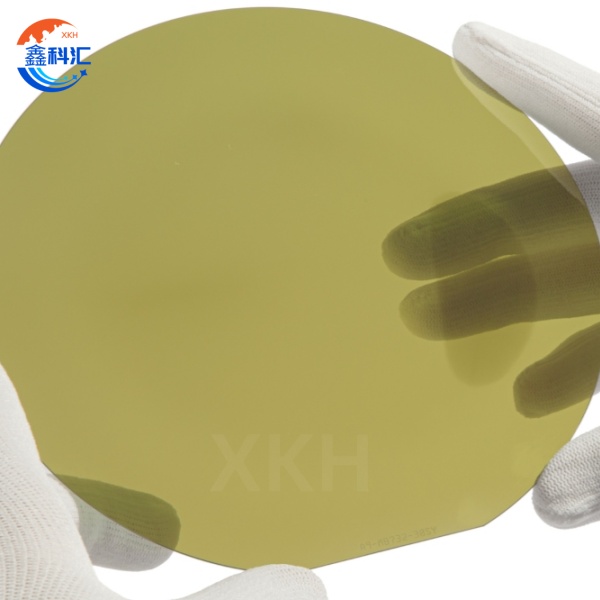
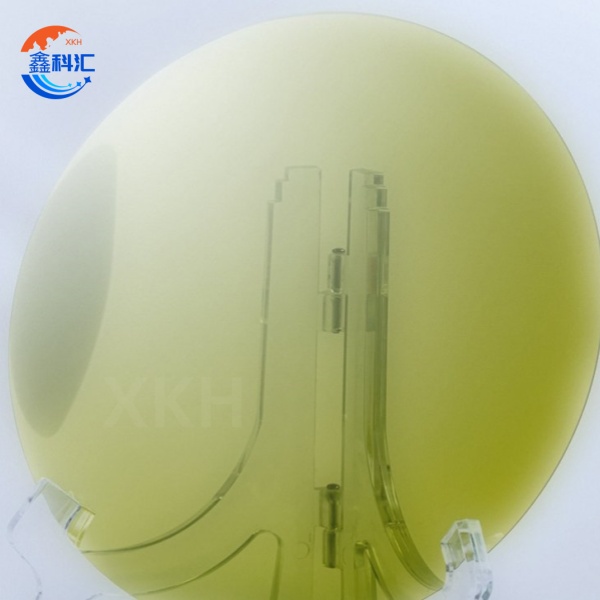