Technologia cięcia wafli, jako kluczowy etap procesu produkcji półprzewodników, jest bezpośrednio powiązana z wydajnością, wydajnością i kosztami produkcji układów scalonych.
#01 Tło i znaczenie krojenia wafli
1.1 Definicja krojenia wafli
Cięcie płytek (znane również jako żłobienie) jest niezbędnym etapem produkcji półprzewodników, mającym na celu podzielenie przetworzonych płytek na wiele indywidualnych matryc. Te matryce zazwyczaj zawierają pełną funkcjonalność obwodu i są głównymi komponentami ostatecznie używanymi w produkcji urządzeń elektronicznych. W miarę jak projekty układów scalonych stają się bardziej złożone, a wymiary nadal się kurczą, wymagania dotyczące precyzji i wydajności dla technologii cięcia płytek stają się coraz bardziej rygorystyczne.
W praktyce krojenie płytek zwykle wykorzystuje narzędzia o wysokiej precyzji, takie jak ostrza diamentowe, aby zapewnić, że każda matryca pozostanie nienaruszona i w pełni funkcjonalna. Kluczowe kroki obejmują przygotowanie przed cięciem, precyzyjną kontrolę podczas procesu cięcia i kontrolę jakości po cięciu.
Przed cięciem wafel musi zostać oznaczony i ustawiony, aby zapewnić dokładne ścieżki cięcia. Podczas cięcia parametry, takie jak nacisk narzędzia i prędkość, muszą być ściśle kontrolowane, aby zapobiec uszkodzeniu wafla. Po cięciu przeprowadzane są kompleksowe kontrole jakości, aby upewnić się, że każdy chip spełnia standardy wydajności.
Podstawowe zasady technologii cięcia płytek obejmują nie tylko wybór sprzętu tnącego i ustawienie parametrów procesu, ale także wpływ właściwości mechanicznych i charakterystyk materiałów na jakość cięcia. Na przykład, płytki krzemowe dielektryczne low-k, ze względu na swoje gorsze właściwości mechaniczne, są bardzo podatne na koncentrację naprężeń podczas cięcia, co prowadzi do awarii, takich jak odpryskiwanie i pękanie. Niska twardość i kruchość materiałów low-k sprawia, że są one bardziej podatne na uszkodzenia strukturalne pod wpływem siły mechanicznej lub naprężeń cieplnych, szczególnie podczas cięcia. Kontakt narzędzia z powierzchnią płytki, w połączeniu z wysokimi temperaturami, może dodatkowo zaostrzyć koncentrację naprężeń.
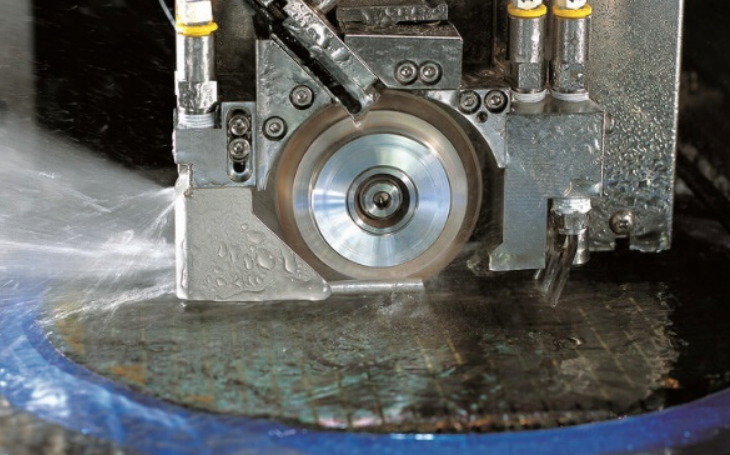
Dzięki postępom w nauce o materiałach technologia cięcia płytek rozszerzyła się poza tradycyjne półprzewodniki na bazie krzemu, obejmując nowe materiały, takie jak azotek galu (GaN). Te nowe materiały, ze względu na swoją twardość i właściwości strukturalne, stawiają nowe wyzwania procesom cięcia, wymagając dalszych udoskonaleń narzędzi i technik cięcia.
Jako kluczowy proces w przemyśle półprzewodnikowym, cięcie płytek jest stale udoskonalane w odpowiedzi na zmieniające się wymagania i postęp technologiczny, kładąc podwaliny pod przyszłe technologie mikroelektroniki i układów scalonych.
Ulepszenia w technologii cięcia płytek wykraczają poza rozwój materiałów pomocniczych i narzędzi. Obejmują one również optymalizację procesu, ulepszenia wydajności sprzętu i precyzyjną kontrolę parametrów cięcia. Te postępy mają na celu zapewnienie wysokiej precyzji, wydajności i stabilności w procesie cięcia płytek, spełniając zapotrzebowanie przemysłu półprzewodnikowego na mniejsze wymiary, większą integrację i bardziej złożone struktury chipów.
Obszar poprawy | Konkretne środki | Ruchomości |
Optymalizacja procesów | - Poprawa wstępnych przygotowań, np. dokładniejsze pozycjonowanie płytek i planowanie ścieżki. | - Zmniejszenie błędów cięcia i poprawa stabilności. |
- Minimalizacja błędów cięcia i poprawa stabilności. | - Wdrożenie mechanizmów monitorowania w czasie rzeczywistym i informacji zwrotnej w celu dostosowania ciśnienia, prędkości i temperatury narzędzi. | |
- Mniejsza podatność na pękanie płytek i poprawa jakości układów scalonych. | ||
Poprawa wydajności sprzętu | - Wykorzystujemy wysoce precyzyjne systemy mechaniczne i zaawansowaną technologię sterowania automatycznego. | - Zwiększ dokładność cięcia i zmniejsz straty materiału. |
- Wprowadzenie technologii cięcia laserowego odpowiedniej do płytek wykonanych z materiałów o dużej twardości. | - Poprawa wydajności produkcji i redukcja błędów ręcznych. | |
- Zwiększenie automatyzacji urządzeń w celu umożliwienia automatycznego monitorowania i regulacji. | ||
Precyzyjna kontrola parametrów | - Precyzyjna regulacja parametrów, takich jak głębokość cięcia, prędkość, typ narzędzia i metody chłodzenia. | - Zapewnić integralność układu i parametry elektryczne. |
- Dostosowywanie parametrów w oparciu o materiał, grubość i strukturę płytki. | - Zwiększ wydajność, zmniejsz ilość odpadów materiałowych i obniż koszty produkcji. | |
Znaczenie strategiczne | - Ciągłe poszukiwanie nowych ścieżek technologicznych, optymalizacja procesów i udoskonalanie możliwości sprzętu w celu sprostania wymaganiom rynku. | - Poprawa wydajności i efektywności produkcji układów scalonych, wsparcie rozwoju nowych materiałów i zaawansowanych projektów układów scalonych. |
1.2 Znaczenie krojenia wafli
Cięcie płytek odgrywa kluczową rolę w procesie produkcji półprzewodników, bezpośrednio wpływając na kolejne kroki, a także na jakość i wydajność produktu końcowego. Jego znaczenie można opisać następująco:
Po pierwsze, dokładność i spójność cięcia są kluczowe dla zapewnienia wydajności i niezawodności chipów. Podczas produkcji wafle przechodzą wiele etapów przetwarzania, aby utworzyć liczne skomplikowane struktury obwodów, które muszą być precyzyjnie podzielone na poszczególne chipy (matryce). Jeśli podczas procesu cięcia wystąpią znaczne błędy w wyrównaniu lub cięciu, obwody mogą zostać uszkodzone, co wpłynie na funkcjonalność i niezawodność chipa. Dlatego technologia cięcia o wysokiej precyzji nie tylko zapewnia integralność każdego chipa, ale także zapobiega uszkodzeniom obwodów wewnętrznych, poprawiając ogólną wydajność.
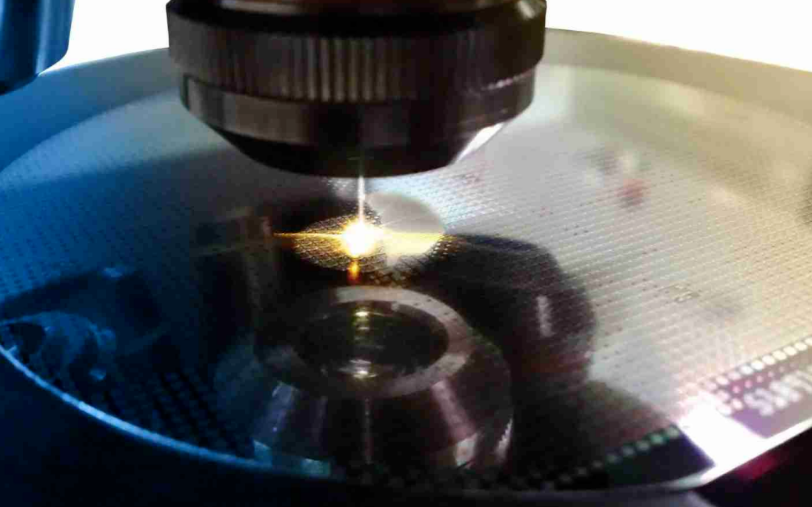
Po drugie, krojenie wafli ma znaczący wpływ na wydajność produkcji i kontrolę kosztów. Jako kluczowy etap procesu produkcyjnego, jego wydajność bezpośrednio wpływa na postęp kolejnych etapów. Poprzez optymalizację procesu krojenia, zwiększenie poziomu automatyzacji i poprawę prędkości cięcia, można znacznie zwiększyć ogólną wydajność produkcji.
Z drugiej strony, marnotrawstwo materiału podczas krojenia jest krytycznym czynnikiem w zarządzaniu kosztami. Wykorzystanie zaawansowanych technologii krojenia nie tylko zmniejsza niepotrzebne straty materiału podczas procesu cięcia, ale także zwiększa wykorzystanie płytek, obniżając tym samym koszty produkcji.
Wraz z postępem w technologii półprzewodników, średnice płytek stale rosną, a gęstość obwodów odpowiednio wzrasta, co stawia wyższe wymagania technologii cięcia. Większe płytki wymagają bardziej precyzyjnej kontroli ścieżek cięcia, szczególnie w obszarach o wysokiej gęstości obwodów, gdzie nawet niewielkie odchylenia mogą spowodować uszkodzenie wielu układów scalonych. Ponadto większe płytki wymagają większej liczby linii cięcia i bardziej złożonych etapów procesu, co wymaga dalszych udoskonaleń w zakresie precyzji, spójności i wydajności technologii cięcia, aby sprostać tym wyzwaniom.
1.3 Proces krojenia wafli
Proces krojenia wafli obejmuje wszystkie etapy od fazy przygotowawczej do końcowej kontroli jakości, przy czym każdy etap jest krytyczny dla zapewnienia jakości i wydajności krojonych chipów. Poniżej znajduje się szczegółowe wyjaśnienie każdej fazy.
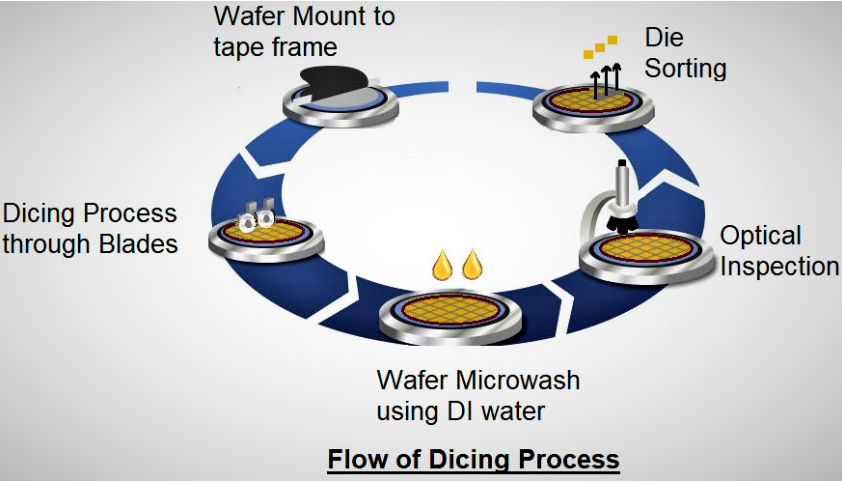
Faza | Szczegółowy opis |
Faza przygotowawcza | -Czyszczenie wafli: Stosuj wodę o wysokiej czystości i specjalistyczne środki czyszczące w połączeniu z szorowaniem ultradźwiękowym lub mechanicznym, aby usunąć zanieczyszczenia, cząsteczki i skażenia, zapewniając czystą powierzchnię. -Precyzyjne pozycjonowanie:Wykorzystaj sprzęt o wysokiej precyzji, aby mieć pewność, że płytka zostanie podzielona dokładnie wzdłuż zaprojektowanych ścieżek cięcia. -Utrwalanie opłatka: Zamocuj płytkę na ramie z taśmy, aby zachować stabilność podczas cięcia i zapobiec uszkodzeniom spowodowanym przez wibracje lub ruch. |
Faza cięcia | -Cięcie ostrzy:Wykorzystują szybkoobrotowe, pokryte diamentem ostrza do cięcia fizycznego, odpowiednie do materiałów na bazie krzemu i ekonomiczne. -Kostkowanie laserowe:Wykorzystują wiązki laserowe o dużej energii do cięcia bezkontaktowego, idealnego do cięcia kruchych lub bardzo twardych materiałów, takich jak azotek galu, zapewniając większą precyzję i mniejsze straty materiału. -Nowe technologie:Wprowadzenie technologii cięcia laserowego i plazmowego w celu dalszego zwiększenia wydajności i precyzji przy jednoczesnym zminimalizowaniu stref narażonych na ciepło. |
Faza czyszczenia | - Użyj wody dejonizowanej (DI) i specjalistycznych środków czyszczących, w połączeniu z czyszczeniem ultradźwiękowym lub natryskowym, aby usunąć zanieczyszczenia i pył powstający podczas cięcia. Zapobiega to wpływowi pozostałości na kolejne procesy lub parametry elektryczne wiórów. - Wysokiej czystości woda dejonizowana zapobiega wprowadzaniu nowych zanieczyszczeń, zapewniając czyste środowisko wafli. |
Faza inspekcji | -Inspekcja optyczna:Wykorzystaj systemy detekcji optycznej połączone z algorytmami AI, aby szybko identyfikować wady, co zapewni brak pęknięć lub wyszczerbień w ciętych wiórach, zwiększy wydajność kontroli i zmniejszy liczbę błędów ludzkich. -Pomiar wymiarów:Sprawdź, czy wymiary układu scalonego spełniają specyfikacje projektowe. -Testowanie wydajności elektrycznej:Zapewniamy, że parametry elektryczne najważniejszych układów scalonych spełniają normy, gwarantując niezawodność w kolejnych zastosowaniach. |
Faza sortowania | - Użyj ramion robotycznych lub przyssawek próżniowych, aby oddzielić zakwalifikowane chipy od ramy taśmy i automatycznie posortować je na podstawie wydajności, zapewniając wydajność i elastyczność produkcji przy jednoczesnym zwiększeniu precyzji. |
Proces cięcia wafli obejmuje czyszczenie, pozycjonowanie, cięcie, czyszczenie, inspekcję i sortowanie wafli, przy czym każdy etap jest krytyczny. Dzięki postępom w automatyzacji, cięciu laserowym i technologiach inspekcji AI nowoczesne systemy cięcia wafli mogą osiągnąć większą precyzję, prędkość i mniejsze straty materiału. W przyszłości nowe technologie cięcia, takie jak laser i plazma, będą stopniowo zastępować tradycyjne cięcie ostrzami, aby sprostać potrzebom coraz bardziej złożonych projektów układów scalonych, co jeszcze bardziej napędza rozwój procesów produkcji półprzewodników.
Technologia cięcia wafli i jej zasady
Na ilustracji przedstawiono trzy powszechnie stosowane technologie cięcia płytek:Cięcie ostrzy,Kostkowanie laserowe, ICięcie plazmowePoniżej znajduje się szczegółowa analiza i dodatkowe wyjaśnienie tych trzech technik:
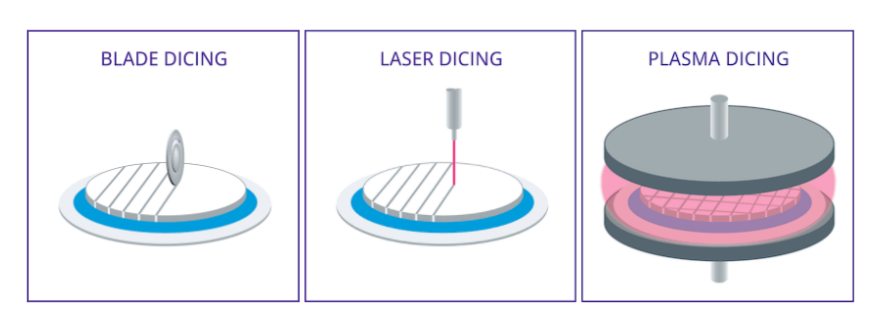
W produkcji półprzewodników cięcie wafli jest kluczowym etapem, który wymaga wybrania odpowiedniej metody cięcia w oparciu o grubość wafli. Pierwszym krokiem jest określenie grubości wafli. Jeśli grubość wafli przekracza 100 mikronów, można wybrać cięcie ostrzowe jako metodę cięcia. Jeśli cięcie ostrzowe nie jest odpowiednie, można zastosować metodę cięcia łamanego, która obejmuje zarówno cięcie rylcem, jak i cięcie ostrzowe.
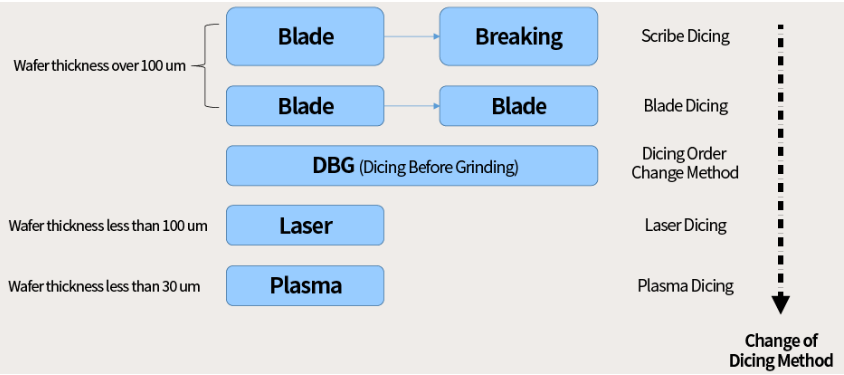
Gdy grubość wafla wynosi od 30 do 100 mikronów, zaleca się metodę DBG (Dice Before Grinding). W takim przypadku można wybrać cięcie rylcem, cięcie ostrzami lub dostosowanie kolejności cięcia w zależności od potrzeb, aby uzyskać najlepsze rezultaty.
W przypadku ultracienkich płytek o grubości mniejszej niż 30 mikronów cięcie laserowe staje się preferowaną metodą ze względu na możliwość precyzyjnego cięcia cienkich płytek bez powodowania nadmiernych uszkodzeń. Jeśli cięcie laserowe nie spełnia określonych wymagań, cięcie plazmowe może być stosowane jako alternatywa. Ten schemat blokowy przedstawia jasną ścieżkę podejmowania decyzji, aby zapewnić wybór najbardziej odpowiedniej technologii cięcia płytek w różnych warunkach grubości.
2.1 Technologia cięcia mechanicznego
Technologia cięcia mechanicznego jest tradycyjną metodą cięcia płytek. Podstawową zasadą jest użycie szybkoobrotowej diamentowej tarczy szlifierskiej jako narzędzia tnącego do krojenia płytek. Kluczowy sprzęt obejmuje wrzeciono z łożyskiem powietrznym, które napędza diamentową tarczę szlifierską z dużą prędkością, aby wykonać precyzyjne cięcie lub rowkowanie wzdłuż wstępnie zdefiniowanej ścieżki cięcia. Technologia ta jest szeroko stosowana w przemyśle ze względu na niski koszt, wysoką wydajność i szerokie zastosowanie.
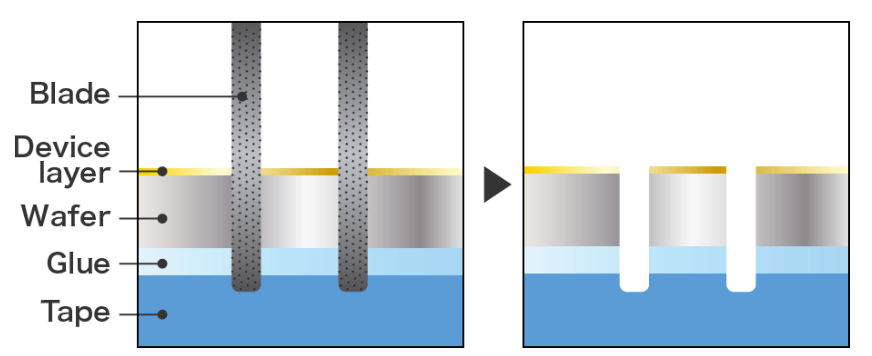
Zalety
Wysoka twardość i odporność na zużycie diamentowych narzędzi ściernych umożliwiają mechaniczną technologię cięcia dostosowaną do potrzeb cięcia różnych materiałów wafli, czy to tradycyjnych materiałów na bazie krzemu, czy nowszych półprzewodników złożonych. Jej obsługa jest prosta, przy stosunkowo niskich wymaganiach technicznych, co dodatkowo zwiększa jej popularność w produkcji masowej. Ponadto, w porównaniu z innymi metodami cięcia, takimi jak cięcie laserowe, cięcie mechaniczne ma bardziej kontrolowane koszty, co czyni je odpowiednim do potrzeb produkcji wielkoseryjnej.
Ograniczenia
Pomimo licznych zalet, technologia cięcia mechanicznego ma również ograniczenia. Po pierwsze, ze względu na fizyczny kontakt między narzędziem a waflem, precyzja cięcia jest stosunkowo ograniczona, co często prowadzi do odchyleń wymiarowych, które mogą mieć wpływ na dokładność późniejszego pakowania i testowania chipów. Po drugie, wady, takie jak odpryski i pęknięcia, mogą łatwo wystąpić podczas procesu cięcia mechanicznego, co nie tylko wpływa na wydajność, ale może również negatywnie wpłynąć na niezawodność i żywotność chipów. Uszkodzenia wywołane naprężeniem mechanicznym są szczególnie szkodliwe dla produkcji chipów o dużej gęstości, zwłaszcza podczas cięcia kruchych materiałów, gdzie problemy te są bardziej widoczne.
Ulepszenia technologiczne
Aby pokonać te ograniczenia, naukowcy nieustannie optymalizują proces cięcia mechanicznego. Kluczowe usprawnienia obejmują udoskonalenie konstrukcji i dobór materiałów ściernic w celu zwiększenia precyzji cięcia i trwałości. Ponadto optymalizacja konstrukcji konstrukcyjnej i systemów sterowania urządzeń tnących dodatkowo poprawiła stabilność i automatyzację procesu cięcia. Te postępy redukują błędy spowodowane przez operacje ludzkie i poprawiają spójność cięć. Wprowadzenie zaawansowanych technologii inspekcji i kontroli jakości w celu monitorowania anomalii w czasie rzeczywistym podczas procesu cięcia również znacznie poprawiło niezawodność cięcia i wydajność.
Przyszły rozwój i nowe technologie
Chociaż technologia cięcia mechanicznego nadal zajmuje znaczącą pozycję w cięciu płytek, nowe technologie cięcia szybko się rozwijają w miarę rozwoju procesów półprzewodnikowych. Na przykład zastosowanie technologii cięcia laserowego termicznego zapewnia nowe rozwiązania problemów precyzji i wad w cięciu mechanicznym. Ta bezkontaktowa metoda cięcia zmniejsza naprężenia fizyczne na płytce, znacznie zmniejszając częstość występowania odprysków i pęknięć, zwłaszcza podczas cięcia bardziej kruchych materiałów. W przyszłości integracja technologii cięcia mechanicznego z nowymi technikami cięcia zapewni produkcji półprzewodników więcej opcji i elastyczności, jeszcze bardziej zwiększając wydajność produkcji i jakość układów scalonych.
Podsumowując, chociaż technologia cięcia mechanicznego ma pewne wady, ciągłe udoskonalenia technologiczne i jej integracja z nowymi technikami cięcia pozwalają jej nadal odgrywać ważną rolę w produkcji półprzewodników i utrzymać konkurencyjność w przyszłych procesach.
2.2 Technologia cięcia laserowego
Technologia cięcia laserowego, jako nowa metoda cięcia płytek, stopniowo zyskała powszechną uwagę w przemyśle półprzewodnikowym ze względu na wysoką precyzję, brak uszkodzeń mechanicznych styków i szybkie możliwości cięcia. Technologia ta wykorzystuje wysoką gęstość energii i zdolność skupiania wiązki laserowej do tworzenia małej strefy wpływu ciepła na powierzchni materiału płytki. Gdy wiązka laserowa jest stosowana do płytki, generowane naprężenie cieplne powoduje pękanie materiału w wyznaczonym miejscu, co pozwala na precyzyjne cięcie.
Zalety technologii cięcia laserowego
• Wysoka precyzjaPrecyzyjne pozycjonowanie wiązki laserowej pozwala na osiągnięcie precyzji cięcia na poziomie mikronów, a nawet nanometrów, spełniając tym samym wymagania nowoczesnej produkcji układów scalonych o wysokiej precyzji i gęstości.
• Brak kontaktu mechanicznego:Cięcie laserowe eliminuje fizyczny kontakt z waflem, zapobiegając tym samym powszechnym problemom podczas cięcia mechanicznego, takim jak odpryskiwanie i pękanie, znacznie zwiększając wydajność i niezawodność układów scalonych.
• Duża prędkość cięciaWysoka prędkość cięcia laserowego przyczynia się do zwiększenia wydajności produkcji, przez co jest ono szczególnie przydatne w scenariuszach produkcji na dużą skalę i z dużą prędkością.
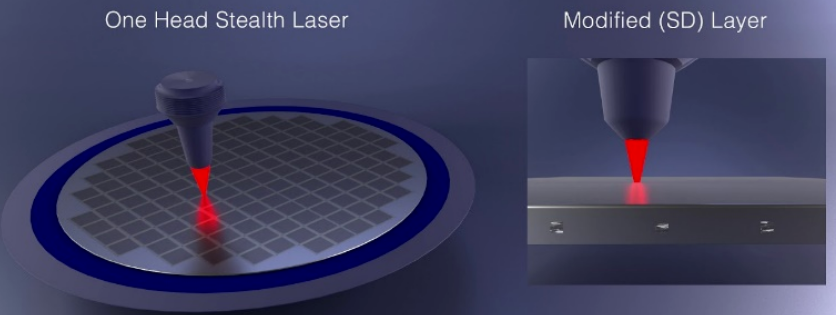
Stawione wyzwania
• Wysoki koszt sprzętuPoczątkowa inwestycja w sprzęt do cięcia laserowego jest wysoka, co wiąże się z presją ekonomiczną, zwłaszcza dla małych i średnich przedsiębiorstw produkcyjnych.
• Kompleksowa kontrola procesówCięcie laserowe wymaga precyzyjnej kontroli kilku parametrów, w tym gęstości energii, położenia ogniska i prędkości cięcia, co czyni ten proces złożonym.
• Problemy ze strefami dotkniętymi ciepłem:Chociaż bezkontaktowy charakter cięcia laserowego zmniejsza uszkodzenia mechaniczne, naprężenie cieplne spowodowane przez strefę wpływu ciepła (HAZ) może negatywnie wpłynąć na właściwości materiału wafla. Aby zminimalizować ten efekt, konieczna jest dalsza optymalizacja procesu.
Kierunki udoskonalenia technologicznego
Aby sprostać tym wyzwaniom, naukowcy skupiają się na obniżaniu kosztów sprzętu, zwiększaniu wydajności cięcia i optymalizacji przepływu procesów.
• Wydajne lasery i systemy optyczne:Dzięki opracowaniu wydajniejszych laserów i zaawansowanych systemów optycznych możliwe jest obniżenie kosztów sprzętu przy jednoczesnym zwiększeniu precyzji i szybkości cięcia.
• Optymalizacja parametrów procesu:Prowadzone są szczegółowe badania nad interakcją laserów z materiałami wafli krzemowych, których celem jest udoskonalenie procesów zmniejszających strefę wpływu ciepła, a tym samym poprawa jakości cięcia.
• Inteligentne systemy sterowania:Rozwój technologii inteligentnego sterowania ma na celu automatyzację i optymalizację procesu cięcia laserowego, zwiększając jego stabilność i spójność.
Technologia cięcia laserowego jest szczególnie skuteczna w przypadku ultracienkich płytek i scenariuszy cięcia o wysokiej precyzji. Wraz ze wzrostem rozmiarów płytek i gęstości obwodów tradycyjne metody cięcia mechanicznego mają trudności ze spełnieniem wymagań dotyczących wysokiej precyzji i wysokiej wydajności nowoczesnej produkcji półprzewodników. Ze względu na swoje unikalne zalety cięcie laserowe staje się preferowanym rozwiązaniem w tych dziedzinach.
Chociaż technologia cięcia laserowego wciąż napotyka wyzwania, takie jak wysokie koszty sprzętu i złożoność procesu, jej unikalne zalety w zakresie wysokiej precyzji i uszkodzeń bezkontaktowych sprawiają, że jest to ważny kierunek rozwoju w produkcji półprzewodników. W miarę postępu technologii laserowej i inteligentnych systemów sterowania oczekuje się, że cięcie laserowe jeszcze bardziej poprawi wydajność i jakość cięcia płytek, napędzając ciągły rozwój przemysłu półprzewodnikowego.
2.3 Technologia cięcia plazmowego
Technologia cięcia plazmowego, jako wschodząca metoda cięcia płytek, zyskała znaczną uwagę w ostatnich latach. Technologia ta wykorzystuje wiązki plazmy o wysokiej energii do precyzyjnego cięcia płytek poprzez kontrolowanie energii, prędkości i ścieżki cięcia wiązki plazmy, co pozwala uzyskać optymalne rezultaty cięcia.
Zasada działania i zalety
Proces cięcia plazmowego opiera się na wysokotemperaturowej, wysokoenergetycznej wiązce plazmy generowanej przez sprzęt. Ta wiązka może ogrzać materiał wafla do punktu topnienia lub parowania w bardzo krótkim czasie, umożliwiając szybkie cięcie. W porównaniu z tradycyjnym cięciem mechanicznym lub laserowym, cięcie plazmowe jest szybsze i wytwarza mniejszą strefę wpływu ciepła, skutecznie zmniejszając występowanie pęknięć i uszkodzeń podczas cięcia.
W praktycznych zastosowaniach technologia cięcia plazmowego jest szczególnie przydatna w przypadku płytek o złożonych kształtach. Jej wysokoenergetyczna, regulowana wiązka plazmy może łatwo ciąć płytki o nieregularnych kształtach z dużą precyzją. Dlatego w produkcji mikroelektroniki, zwłaszcza w produkcji dostosowanej i małoseryjnej wysokiej klasy chipów, technologia ta wykazuje duże nadzieje na szerokie zastosowanie.
Wyzwania i ograniczenia
Pomimo licznych zalet technologii cięcia plazmowego, wiąże się ona również z pewnymi wyzwaniami.
• Proces złożonyProces cięcia plazmowego jest złożony i wymaga precyzyjnego sprzętu oraz doświadczonych operatorów, aby zapewnićdokładność i stabilność cięcia.
• Kontrola środowiska i bezpieczeństwo:Wysoka temperatura i energia wiązki plazmowej wymagają rygorystycznej kontroli środowiskowej i środków bezpieczeństwa, co zwiększa złożoność i koszt wdrożenia.
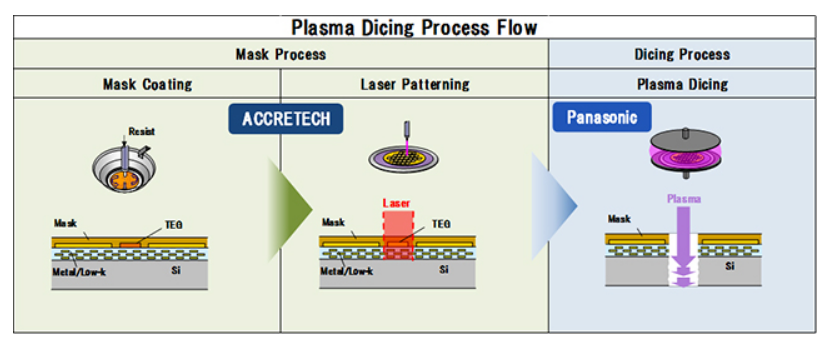
Przyszłe kierunki rozwoju
Wraz z postępem technologicznym oczekuje się, że wyzwania związane z cięciem plazmowym zostaną stopniowo pokonane. Poprzez opracowanie inteligentniejszego i bardziej stabilnego sprzętu do cięcia można zmniejszyć zależność od operacji ręcznych, co poprawi wydajność produkcji. Jednocześnie optymalizacja parametrów procesu i środowiska cięcia pomoże obniżyć ryzyko bezpieczeństwa i koszty operacyjne.
W przemyśle półprzewodnikowym innowacje w technologii cięcia i krojenia płytek są kluczowe dla rozwoju branży. Technologia cięcia plazmowego, z jej wysoką precyzją, wydajnością i zdolnością do obsługi złożonych kształtów płytek, wyłoniła się jako znaczący nowy gracz w tej dziedzinie. Chociaż nadal istnieją pewne wyzwania, problemy te będą stopniowo rozwiązywane dzięki ciągłym innowacjom technologicznym, które przyniosą więcej możliwości i okazji do produkcji półprzewodników.
Perspektywy zastosowania technologii cięcia plazmowego są ogromne i oczekuje się, że odegra ona ważniejszą rolę w produkcji półprzewodników w przyszłości. Dzięki ciągłej innowacji technologicznej i optymalizacji cięcie plazmowe nie tylko rozwiąże istniejące wyzwania, ale także stanie się potężnym motorem wzrostu przemysłu półprzewodników.
2.4 Jakość cięcia i czynniki wpływające
Jakość cięcia wafli jest krytyczna dla późniejszego pakowania chipów, testowania oraz ogólnej wydajności i niezawodności produktu końcowego. Typowe problemy napotykane podczas cięcia obejmują pęknięcia, odpryskiwanie i odchylenia cięcia. Na problemy te wpływa kilka czynników działających razem.
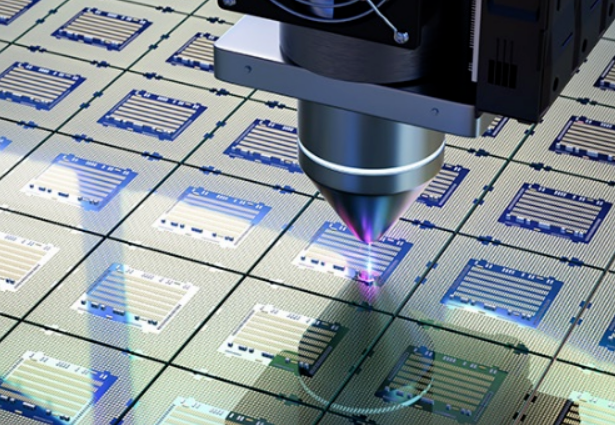
Kategoria | Treść | Uderzenie |
Parametry procesu | Prędkość cięcia, posuw i głębokość cięcia bezpośrednio wpływają na stabilność i precyzję procesu cięcia. Nieprawidłowe ustawienia mogą prowadzić do koncentracji naprężeń i nadmiernej strefy wpływu ciepła, co skutkuje pęknięciami i odpryskami. Odpowiednie dostosowanie parametrów w oparciu o materiał wafla, grubość i wymagania dotyczące cięcia jest kluczowe dla osiągnięcia pożądanych rezultatów cięcia. | Prawidłowe parametry procesu gwarantują precyzyjne cięcie i redukują ryzyko wystąpienia wad, takich jak pęknięcia i odpryski. |
Czynniki sprzętowe i materiałowe | -Jakość ostrza: Materiał, twardość i odporność na zużycie ostrza wpływają na płynność procesu cięcia i płaskość powierzchni cięcia. Ostrza niskiej jakości zwiększają tarcie i naprężenia termiczne, co może prowadzić do pęknięć lub odprysków. Wybór odpowiedniego materiału ostrza ma kluczowe znaczenie. -Wydajność chłodziwa: Chłodziwa pomagają obniżyć temperaturę cięcia, zminimalizować tarcie i usunąć zanieczyszczenia. Nieskuteczne chłodziwo może prowadzić do wysokich temperatur i gromadzenia się zanieczyszczeń, co wpływa na jakość cięcia i wydajność. Wybór wydajnych i przyjaznych dla środowiska chłodziw jest kluczowy. | Jakość ostrza wpływa na precyzję i gładkość cięcia. Nieskuteczne chłodziwo może skutkować słabą jakością cięcia i wydajnością, co podkreśla potrzebę optymalnego wykorzystania chłodziwa. |
Kontrola Procesów i Inspekcja Jakości | -Kontrola procesu:Monitorowanie w czasie rzeczywistym i dostosowywanie parametrów cięcia kluczy w celu zapewnienia stabilności i spójności procesu cięcia. -Kontrola jakości:Kontrola wyglądu, pomiary wymiarów i testy wydajności elektrycznej po cięciu pozwalają na szybką identyfikację i rozwiązanie problemów jakościowych, zwiększając dokładność i spójność cięcia. | Właściwa kontrola procesu i kontrola jakości pomagają zapewnić spójne, wysokiej jakości rezultaty cięcia i wczesne wykrywanie potencjalnych problemów. |

Poprawa jakości cięcia
Poprawa jakości cięcia wymaga kompleksowego podejścia, które uwzględnia parametry procesu, dobór sprzętu i materiałów, kontrolę procesu i inspekcję. Poprzez ciągłe udoskonalanie technologii cięcia i optymalizację metod procesu można jeszcze bardziej zwiększyć precyzję i stabilność cięcia płytek, zapewniając bardziej niezawodne wsparcie techniczne dla przemysłu produkcji półprzewodników.
#03 Postępowanie i testowanie po cięciu
3.1 Czyszczenie i suszenie
Czyszczenie i suszenie po cięciu wafli są kluczowe dla zapewnienia jakości chipa i płynnego przebiegu kolejnych procesów. Na tym etapie konieczne jest dokładne usunięcie resztek krzemu, pozostałości chłodziwa i innych zanieczyszczeń powstałych podczas cięcia. Równie ważne jest upewnienie się, że chipy nie zostaną uszkodzone podczas procesu czyszczenia, a po wysuszeniu upewnienie się, że na powierzchni chipa nie pozostaje wilgoć, aby zapobiec problemom, takim jak korozja lub wyładowania elektrostatyczne.
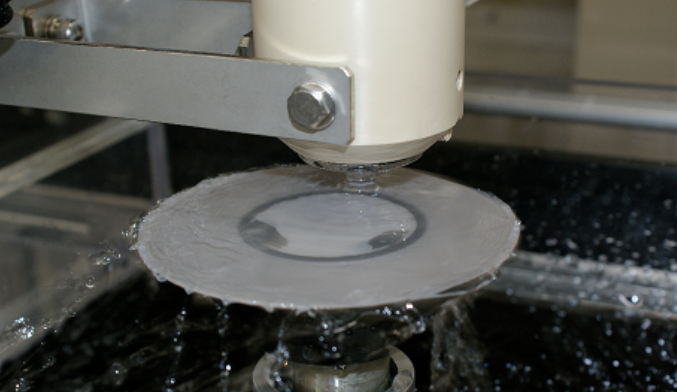
Postępowanie po cięciu: proces czyszczenia i suszenia
Krok procesu | Treść | Uderzenie |
Proces czyszczenia | -Metoda: Do czyszczenia należy używać specjalistycznych środków czyszczących oraz czystej wody, w połączeniu z ultradźwiękowymi lub mechanicznymi technikami szczotkowania. | Zapewnia dokładne usuwanie zanieczyszczeń i zapobiega uszkodzeniu wiórów podczas czyszczenia. |
-Wybór środka czyszczącego: Dokonaj wyboru w oparciu o materiał płytki i rodzaj zanieczyszczeń, aby zapewnić skuteczne czyszczenie bez uszkodzenia układu scalonego. | Wybór właściwego środka jest kluczowy dla skutecznego czyszczenia i ochrony przed odpryskami. | |
-Kontrola parametrów:Należy ściśle kontrolować temperaturę czyszczenia, czas i stężenie środka czyszczącego, aby zapobiec problemom jakościowym spowodowanym przez niewłaściwe czyszczenie. | Kontrola pomaga uniknąć uszkodzenia płytki lub pozostawienia zanieczyszczeń, zapewniając tym samym stałą jakość. | |
Proces suszenia | -Tradycyjne metody:Suszenie naturalnym powietrzem i suszenie gorącym powietrzem mają niską wydajność i mogą prowadzić do gromadzenia się elektryczności statycznej. | Może skutkować dłuższym czasem schnięcia i potencjalnymi problemami ze statycznością. |
-Nowoczesne technologie:Wykorzystujemy zaawansowane technologie, takie jak suszenie próżniowe i suszenie na podczerwień, aby zapewnić szybkie schnięcie wiórów i uniknąć szkodliwych efektów. | Szybszy i bardziej wydajny proces suszenia, zmniejszający ryzyko wystąpienia wyładowań elektrostatycznych lub problemów związanych z wilgocią. | |
Wybór i konserwacja sprzętu | -Wybór sprzętu:Wysokowydajne urządzenia czyszczące i suszące zwiększają efektywność przetwarzania i pozwalają na dokładną kontrolę potencjalnych problemów podczas obsługi. | Wysokiej jakości maszyny zapewniają lepszą obróbkę i zmniejszają prawdopodobieństwo wystąpienia błędów podczas czyszczenia i suszenia. |
-Konserwacja sprzętu:Regularne kontrole i konserwacja sprzętu zapewniają jego optymalny stan roboczy, gwarantując jakość wiórów. | Właściwa konserwacja zapobiega awariom sprzętu, gwarantując niezawodność i wysoką jakość przetwarzania. |
Czyszczenie i suszenie po cięciu
Czyszczenie i suszenie po cięciu wafli to złożone i delikatne procesy, które wymagają starannego rozważenia wielu czynników, aby zapewnić końcowy wynik przetwarzania. Dzięki zastosowaniu naukowych metod i rygorystycznych procedur możliwe jest zapewnienie, że każdy chip wejdzie na kolejne etapy pakowania i testowania w optymalnym stanie.
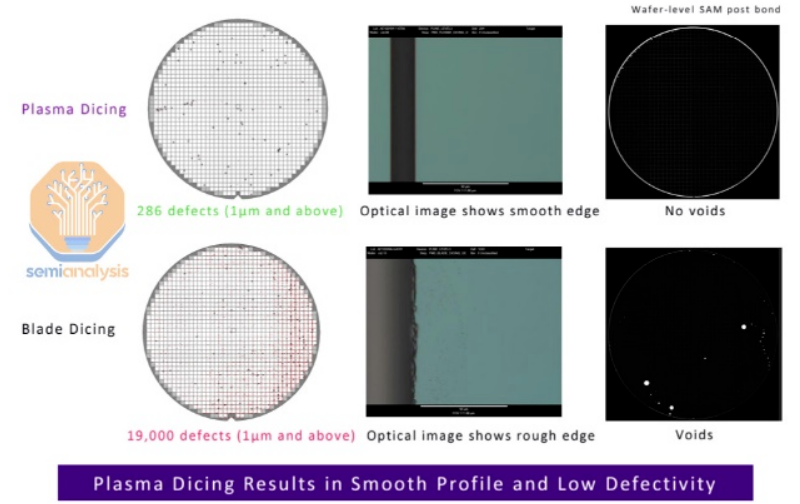
Kontrola i testowanie po cięciu
Krok | Treść | Uderzenie |
Krok inspekcji | 1.Kontrola wizualna: Użyj wizualnego lub zautomatyzowanego sprzętu inspekcyjnego, aby sprawdzić widoczne wady, takie jak pęknięcia, odpryski lub zanieczyszczenia na powierzchni chipa. Szybko zidentyfikuj fizycznie uszkodzone chipy, aby uniknąć marnotrawstwa. | Pomaga w identyfikacji i eliminacji wadliwych wiórów na wczesnym etapie procesu, zmniejszając straty materiału. |
2.Pomiar rozmiaru:Używaj precyzyjnych urządzeń pomiarowych do dokładnego pomiaru wymiarów układów scalonych, co zapewni, że rozmiar cięcia będzie zgodny ze specyfikacją projektu i zapobiegnie problemom z wydajnością lub trudnościom w pakowaniu. | Zapewnia, że rozmiary chipów mieszczą się w wymaganych granicach, zapobiegając pogorszeniu wydajności lub problemom z montażem. | |
3.Testowanie wydajności elektrycznej:Oceń kluczowe parametry elektryczne, takie jak rezystancja, pojemność i indukcyjność, aby zidentyfikować niezgodne układy scalone i upewnić się, że do następnego etapu przejdą tylko układy o zakwalifikowanej wydajności. | Gwarantuje, że do procesu przechodzą wyłącznie funkcjonalne i przetestowane pod kątem wydajności układy scalone, co zmniejsza ryzyko awarii na późniejszych etapach. | |
Krok testowy | 1.Testowanie funkcjonalne:Sprawdź, czy podstawowe funkcje układu scalonego działają zgodnie z oczekiwaniami, identyfikując i eliminując układy scalone z nieprawidłowościami funkcjonalnymi. | Gwarantuje, że układy scalone spełniają podstawowe wymagania operacyjne przed przejściem do dalszych etapów. |
2.Testowanie niezawodności:Ocena stabilności działania układu scalonego przy długotrwałym użytkowaniu lub w trudnych warunkach, zwykle obejmująca starzenie w wysokiej temperaturze, testy w niskiej temperaturze i testy wilgotności w celu symulacji ekstremalnych warunków rzeczywistych. | Zapewnia niezawodną pracę układów scalonych w różnych warunkach środowiskowych, wydłużając żywotność i stabilność produktu. | |
3.Testowanie zgodności:Sprawdź, czy układ scalony działa prawidłowo z innymi komponentami lub systemami, upewniając się, że nie występują żadne błędy lub pogorszenie wydajności z powodu braku kompatybilności. | Zapewnia płynną pracę w rzeczywistych zastosowaniach, zapobiegając problemom ze zgodnością. |
3.3 Opakowanie i przechowywanie
Po cięciu wafli chipy są kluczowym elementem procesu produkcji półprzewodników, a ich etapy pakowania i przechowywania są równie ważne. Prawidłowe środki pakowania i przechowywania są niezbędne nie tylko do zapewnienia bezpieczeństwa i stabilności chipów podczas transportu i przechowywania, ale także do zapewnienia silnego wsparcia dla kolejnych etapów produkcji, testowania i pakowania.
Podsumowanie etapów kontroli i testów:
Kroki inspekcji i testowania układów scalonych po cięciu wafli obejmują szereg aspektów, w tym inspekcję wizualną, pomiar rozmiaru, testowanie wydajności elektrycznej, testowanie funkcjonalne, testowanie niezawodności i testowanie zgodności. Kroki te są ze sobą powiązane i wzajemnie się uzupełniają, tworząc solidną barierę zapewniającą jakość i niezawodność produktu. Dzięki ścisłym procedurom inspekcji i testowania potencjalne problemy można szybko zidentyfikować i rozwiązać, zapewniając, że produkt końcowy spełnia wymagania i oczekiwania klienta.
Aspekt | Treść |
Środki opakowaniowe | 1.Antystatyczny:Materiały opakowaniowe powinny mieć doskonałe właściwości antystatyczne, aby zapobiegać uszkodzeniom urządzeń spowodowanym przez elektryczność statyczną lub wpływowi na ich wydajność. |
2.Odporny na wilgoć:Materiały opakowaniowe powinny charakteryzować się dobrą odpornością na wilgoć, aby zapobiec korozji i pogorszeniu parametrów elektrycznych spowodowanych wilgocią. | |
3.Odporny na wstrząsy:Materiały opakowaniowe powinny zapewniać skuteczną amortyzację wstrząsów, aby chronić chipy przed wibracjami i uderzeniami podczas transportu. | |
Środowisko przechowywania | 1.Kontrola wilgotności:Należy ściśle kontrolować wilgotność powietrza, utrzymując ją w odpowiednim zakresie, aby zapobiec absorpcji wilgoci i korozji spowodowanej nadmierną wilgotnością lub problemom ze statycznością spowodowanym przez niską wilgotność. |
2.Czystość:Utrzymuj czyste środowisko przechowywania, aby zapobiec zanieczyszczeniu wiórów kurzem i zanieczyszczeniami. | |
3.Kontrola temperatury:Ustaw rozsądny zakres temperatur i utrzymuj ich stabilność, aby zapobiec przyspieszonemu starzeniu się z powodu nadmiernego ciepła lub problemów z kondensacją wywołanych przez niskie temperatury. | |
Regularna kontrola | Regularnie sprawdzaj i oceniaj przechowywane chipy, stosując inspekcje wizualne, pomiary wielkości i testy wydajności elektrycznej, aby identyfikować i rozwiązywać potencjalne problemy w odpowiednim czasie. Na podstawie czasu i warunków przechowywania zaplanuj wykorzystanie chipów, aby upewnić się, że są używane w optymalnym stanie. |
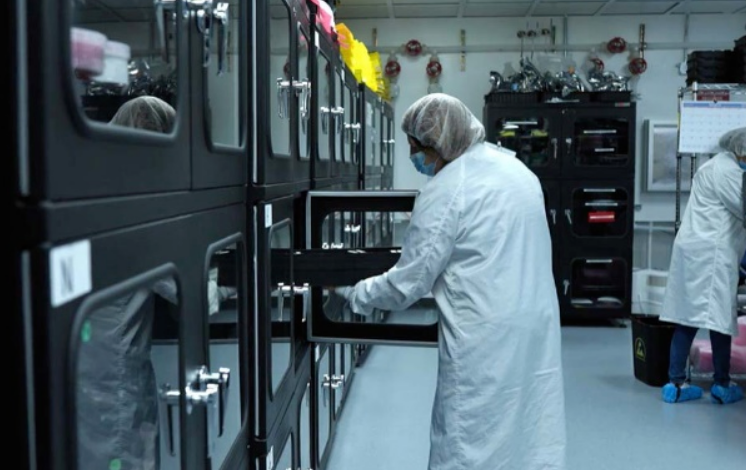
Problem mikropęknięć i uszkodzeń podczas procesu cięcia płytek jest poważnym wyzwaniem w produkcji półprzewodników. Naprężenie tnące jest główną przyczyną tego zjawiska, ponieważ powoduje drobne pęknięcia i uszkodzenia na powierzchni płytki, co prowadzi do wzrostu kosztów produkcji i spadku jakości produktu.
Aby sprostać temu wyzwaniu, kluczowe jest zminimalizowanie naprężeń podczas cięcia i wdrożenie zoptymalizowanych technik cięcia, narzędzi i warunków. Staranne zwrócenie uwagi na czynniki takie jak materiał ostrza, prędkość cięcia, ciśnienie i metody chłodzenia może pomóc w zmniejszeniu powstawania mikropęknięć i poprawie ogólnej wydajności procesu. Ponadto trwające badania nad bardziej zaawansowanymi technologiami cięcia, takimi jak cięcie laserowe, badają sposoby dalszego łagodzenia tych problemów.
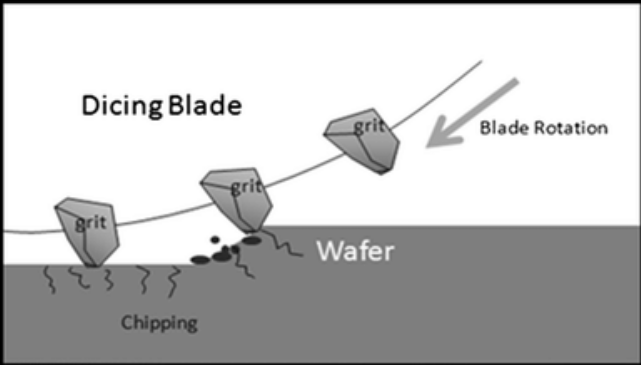
Jako kruchy materiał, wafle są podatne na wewnętrzne zmiany strukturalne, gdy są poddawane naprężeniom mechanicznym, termicznym lub chemicznym, co prowadzi do powstawania mikropęknięć. Chociaż pęknięcia te mogą nie być od razu zauważalne, mogą się rozszerzać i powodować poważniejsze uszkodzenia w miarę postępu procesu produkcyjnego. Problem ten staje się szczególnie problematyczny podczas kolejnych etapów pakowania i testowania, gdzie wahania temperatury i dodatkowe naprężenia mechaniczne mogą powodować, że te mikropęknięcia przekształcą się w widoczne pęknięcia, co potencjalnie prowadzi do awarii chipa.
Aby złagodzić to ryzyko, konieczne jest dokładne kontrolowanie procesu cięcia poprzez optymalizację parametrów, takich jak prędkość cięcia, ciśnienie i temperatura. Stosowanie mniej agresywnych metod cięcia, takich jak cięcie laserowe, może zmniejszyć naprężenie mechaniczne wafla i zminimalizować powstawanie mikropęknięć. Ponadto wdrożenie zaawansowanych metod inspekcji, takich jak skanowanie w podczerwieni lub obrazowanie rentgenowskie podczas procesu cięcia wafla, może pomóc wykryć te pęknięcia na wczesnym etapie, zanim spowodują dalsze uszkodzenia.
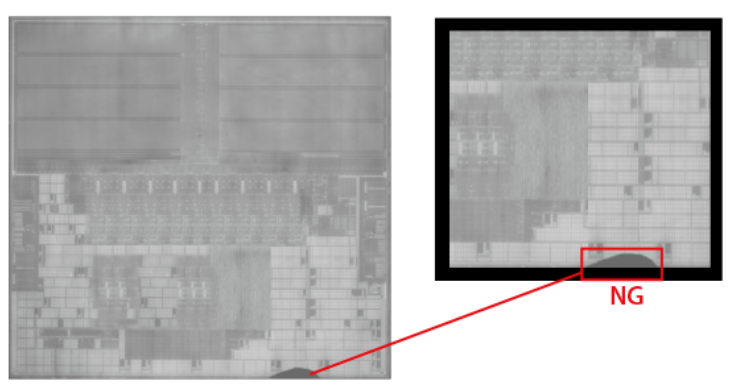
Uszkodzenie powierzchni wafla jest poważnym problemem w procesie cięcia, ponieważ może mieć bezpośredni wpływ na wydajność i niezawodność układu. Takie uszkodzenia mogą być spowodowane niewłaściwym użyciem narzędzi tnących, nieprawidłowymi parametrami cięcia lub wadami materiału wrodzonymi w samym waflu. Niezależnie od przyczyny, uszkodzenia te mogą prowadzić do zmian rezystancji elektrycznej lub pojemności obwodu, co wpływa na ogólną wydajność.
Aby rozwiązać te problemy, rozważane są dwie kluczowe strategie:
1. Optymalizacja narzędzi skrawających i parametrów:Dzięki stosowaniu ostrzejszych ostrzy, regulacji prędkości cięcia i modyfikacji głębokości cięcia można zminimalizować koncentrację naprężeń w trakcie procesu cięcia, co zmniejsza ryzyko uszkodzeń.
2. Eksploracja nowych technologii cięcia: Zaawansowane techniki, takie jak cięcie laserowe i cięcie plazmowe, oferują zwiększoną precyzję, a jednocześnie potencjalnie zmniejszają poziom uszkodzeń wafla. Technologie te są badane w celu znalezienia sposobów na osiągnięcie wysokiej dokładności cięcia przy jednoczesnym zminimalizowaniu naprężeń termicznych i mechanicznych wafla.
Obszar oddziaływania termicznego i jego wpływ na wydajność
W procesach cięcia termicznego, takich jak cięcie laserowe i plazmowe, wysokie temperatury nieuchronnie tworzą strefę uderzenia termicznego na powierzchni wafla. Obszar ten, w którym gradient temperatury jest znaczny, może zmienić właściwości materiału, wpływając na ostateczną wydajność układu scalonego.
Wpływ strefy wpływu termicznego (TAZ):
Zmiany w strukturze kryształu:W wysokich temperaturach atomy w materiale wafla mogą się przegrupować, powodując zniekształcenia w strukturze krystalicznej. To zniekształcenie osłabia materiał, zmniejszając jego wytrzymałość mechaniczną i stabilność, co zwiększa ryzyko awarii układu scalonego podczas użytkowania.
Zmiany właściwości elektrycznych:Wysokie temperatury mogą zmieniać stężenie nośników i ruchliwość w materiałach półprzewodnikowych, wpływając na przewodnictwo elektryczne układu scalonego i wydajność przesyłu prądu. Zmiany te mogą prowadzić do spadku wydajności układu scalonego, co potencjalnie czyni go nieprzydatnym do zamierzonego celu.
Aby złagodzić te skutki, należy kontrolować temperaturę podczas cięcia, optymalizować parametry cięcia i stosować takie metody, jak strumienie chłodzące lub zabiegi po obróbce. Są to podstawowe strategie pozwalające ograniczyć zakres oddziaływania termicznego i zachować integralność materiału.
Ogólnie rzecz biorąc, zarówno mikropęknięcia, jak i strefy uderzeń termicznych stanowią kluczowe wyzwania w technologii cięcia płytek. Dalsze badania, obok postępu technologicznego i środków kontroli jakości, będą konieczne, aby poprawić jakość produktów półprzewodnikowych i zwiększyć ich konkurencyjność rynkową.
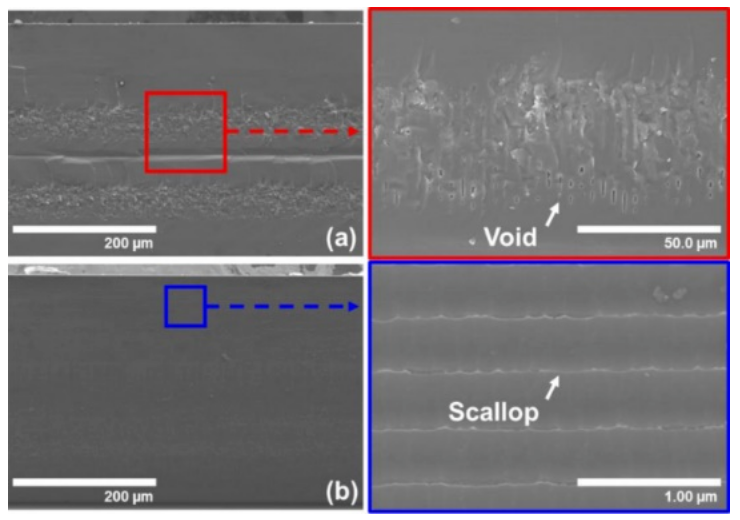
Środki służące kontroli strefy oddziaływania termicznego:
Optymalizacja parametrów procesu cięcia:Zmniejszenie prędkości i mocy cięcia może skutecznie zminimalizować rozmiar strefy uderzenia termicznego (TAZ). Pomaga to kontrolować ilość ciepła wytwarzanego podczas procesu cięcia, co bezpośrednio wpływa na właściwości materiałowe wafla.
Zaawansowane technologie chłodzenia:Zastosowanie technologii, takich jak chłodzenie ciekłym azotem i chłodzenie mikroprzepływowe, może znacznie ograniczyć zasięg strefy oddziaływania termicznego. Te metody chłodzenia pomagają wydajniej rozpraszać ciepło, zachowując w ten sposób właściwości materiału wafla i minimalizując uszkodzenia termiczne.
Wybór materiałów:Naukowcy badają nowe materiały, takie jak nanorurki węglowe i grafen, które posiadają doskonałą przewodność cieplną i wytrzymałość mechaniczną. Materiały te mogą zmniejszyć strefę uderzenia termicznego, jednocześnie poprawiając ogólną wydajność chipów.
Podsumowując, chociaż strefa oddziaływania termicznego jest nieuniknioną konsekwencją technologii cięcia termicznego, można ją skutecznie kontrolować za pomocą zoptymalizowanych technik przetwarzania i doboru materiałów. Przyszłe badania prawdopodobnie skupią się na dostrajaniu i automatyzacji procesów cięcia termicznego w celu uzyskania bardziej wydajnego i precyzyjnego cięcia płytek.

Strategia równowagi:
Osiągnięcie optymalnej równowagi między wydajnością wafli a wydajnością produkcji jest ciągłym wyzwaniem w technologii cięcia wafli. Producenci muszą brać pod uwagę wiele czynników, takich jak popyt rynkowy, koszty produkcji i jakość produktu, aby opracować racjonalną strategię produkcji i parametry procesu. Jednocześnie wprowadzenie zaawansowanego sprzętu tnącego, poprawa umiejętności operatora i poprawa kontroli jakości surowca są niezbędne do utrzymania lub nawet poprawy wydajności przy jednoczesnym zwiększeniu wydajności produkcji.
Przyszłe wyzwania i możliwości:
Wraz z rozwojem technologii półprzewodnikowej cięcie płytek napotyka nowe wyzwania i możliwości. Wraz ze zmniejszaniem się rozmiarów chipów i wzrostem integracji, wymagania dotyczące precyzji i jakości cięcia znacznie rosną. Jednocześnie pojawiające się technologie dostarczają nowych pomysłów na rozwój technik cięcia płytek. Producenci muszą być na bieżąco z dynamiką rynku i trendami technologicznymi, stale dostosowując i optymalizując strategie produkcji i parametry procesu, aby sprostać zmianom rynkowym i wymaganiom technologicznym.
Podsumowując, poprzez uwzględnienie kwestii popytu rynkowego, kosztów produkcji i jakości produktu oraz poprzez wprowadzenie zaawansowanego sprzętu i technologii, podniesienie umiejętności operatorów i wzmocnienie kontroli nad surowcami, producenci mogą osiągnąć najlepszą równowagę pomiędzy wydajnością płytek a efektywnością produkcji podczas ich cięcia, co przekłada się na wydajną i wysokiej jakości produkcję produktów półprzewodnikowych.
Perspektywy na przyszłość:
Dzięki szybkiemu postępowi technologicznemu technologia półprzewodników rozwija się w niespotykanym dotąd tempie. Jako kluczowy krok w produkcji półprzewodników, technologia cięcia płytek jest gotowa na ekscytujące nowe osiągnięcia. Patrząc w przyszłość, oczekuje się, że technologia cięcia płytek osiągnie znaczące ulepszenia w zakresie precyzji, wydajności i kosztów, wstrzykując nową witalność do ciągłego wzrostu przemysłu półprzewodników.
Zwiększanie precyzji:
W dążeniu do większej precyzji technologia cięcia płytek będzie nieustannie przesuwać granice istniejących procesów. Poprzez dogłębne badanie mechanizmów fizycznych i chemicznych procesu cięcia oraz precyzyjną kontrolę parametrów cięcia, można osiągnąć dokładniejsze wyniki cięcia, aby sprostać coraz bardziej złożonym wymaganiom projektowania obwodów. Ponadto eksploracja nowych materiałów i metod cięcia znacznie poprawi wydajność i jakość.
Zwiększanie efektywności:
Nowe urządzenia do cięcia płytek będą koncentrować się na inteligentnym i zautomatyzowanym projektowaniu. Wprowadzenie zaawansowanych systemów sterowania i algorytmów umożliwi urządzeniom automatyczne dostosowywanie parametrów cięcia do różnych materiałów i wymagań projektowych, co znacznie zwiększy wydajność produkcji. Innowacje, takie jak technologia cięcia wielu płytek i systemy szybkiej wymiany ostrzy, odegrają kluczową rolę w zwiększaniu wydajności.
Redukcja kosztów:
Redukcja kosztów jest kluczowym kierunkiem rozwoju technologii cięcia płytek. Wraz z rozwojem nowych materiałów i metod cięcia oczekuje się, że koszty sprzętu i wydatki na konserwację będą skutecznie kontrolowane. Ponadto optymalizacja procesów produkcyjnych i redukcja liczby złomów jeszcze bardziej zmniejszą ilość odpadów podczas produkcji, co doprowadzi do zmniejszenia ogólnych kosztów produkcji.
Inteligentna produkcja i IoT:
Integracja inteligentnej produkcji i technologii Internetu rzeczy (IoT) przyniesie transformacyjne zmiany w technologii cięcia płytek. Dzięki łączności i udostępnianiu danych między urządzeniami każdy etap procesu produkcyjnego można monitorować i optymalizować w czasie rzeczywistym. To nie tylko poprawia wydajność produkcji i jakość produktu, ale także zapewnia firmom dokładniejsze prognozowanie rynku i wsparcie w podejmowaniu decyzji.
W przyszłości technologia cięcia płytek poczyni niezwykłe postępy w precyzji, wydajności i kosztach. Postępy te będą napędzać dalszy rozwój przemysłu półprzewodników i wniosą więcej innowacji technologicznych i udogodnień do ludzkiego społeczeństwa.
Czas publikacji: 19-11-2024