Czyszczenie na mokro (Wet Clean) to jeden z najważniejszych etapów procesów produkcji półprzewodników, mający na celu usunięcie różnych zanieczyszczeń z powierzchni płytki, aby mieć pewność, że kolejne etapy procesu będą mogły być przeprowadzane na czystej powierzchni.
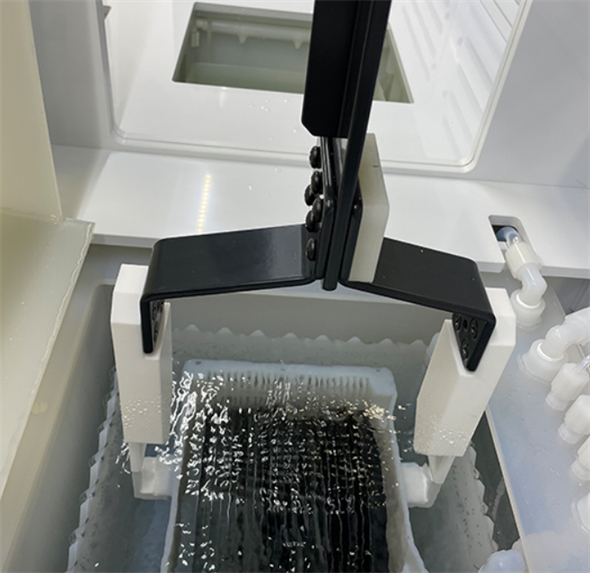
Wraz ze zmniejszaniem się rozmiarów układów półprzewodnikowych i wzrostem wymagań dotyczących precyzji, wymagania techniczne dotyczące procesów czyszczenia płytek półprzewodnikowych stają się coraz bardziej rygorystyczne. Nawet najmniejsze cząsteczki, materiały organiczne, jony metali lub pozostałości tlenków na powierzchni płytki mogą znacząco wpłynąć na wydajność urządzenia, a tym samym na jego wydajność i niezawodność.
Podstawowe zasady czyszczenia płytek
Istotą czyszczenia wafli półprzewodnikowych jest skuteczne usuwanie różnych zanieczyszczeń z ich powierzchni za pomocą metod fizycznych, chemicznych i innych, co zapewnia, że wafel ma czystą powierzchnię nadającą się do dalszej obróbki.
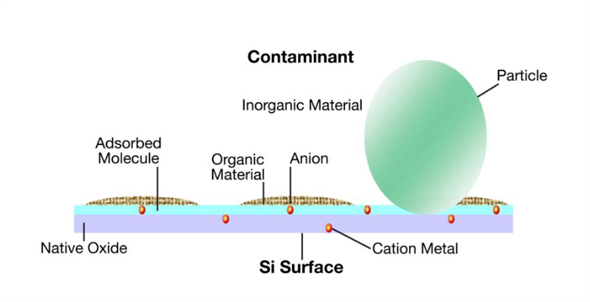
Rodzaj zanieczyszczenia
Główne czynniki wpływające na charakterystykę urządzenia
Zanieczyszczenie artykułu | Wady wzoru
Wady implantacji jonów
Wady wynikające z przebicia folii izolacyjnej
| |
Zanieczyszczenie metaliczne | Metale alkaliczne | Niestabilność tranzystora MOS
Rozpad/degradacja warstwy tlenku bramki
|
Metale ciężkie | Zwiększony prąd upływu wstecznego złącza PN
Wady wynikające z uszkodzenia warstwy tlenkowej bramki
Degradacja żywotności nośników mniejszościowych
Generowanie defektów w warstwie wzbudzenia tlenkowego
| |
Zanieczyszczenie chemiczne | Materiał organiczny | Wady wynikające z uszkodzenia warstwy tlenkowej bramki
Wariacje na temat filmów CVD (czasy inkubacji)
Zmiany grubości warstwy tlenku termicznego (przyspieszone utlenianie)
Występowanie zmętnienia (płytka, soczewka, lustro, maska, siatka)
|
Domieszki nieorganiczne (B, P) | Przesunięcie Vth tranzystora MOS
Zmiany rezystancji podłoża krzemowego i arkusza polikrzemowego o wysokiej rezystancji
| |
Zasady nieorganiczne (aminy, amoniak) i kwasy (SOx) | Degradacja rozdzielczości rezystów wzmacnianych chemicznie
Występowanie zanieczyszczeń cząsteczkowych i zamglenia w wyniku wytwarzania soli
| |
Warstwy tlenków naturalnych i chemicznych powstające w wyniku działania wilgoci i powietrza | Zwiększona rezystancja styku
Rozpad/degradacja warstwy tlenku bramki
|
Cele czyszczenia płytek obejmują w szczególności:
Usuwanie cząstek: Usunięcie małych cząstek przyczepionych do powierzchni płytki półprzewodnikowej za pomocą metod fizycznych lub chemicznych. Mniejsze cząstki są trudniejsze do usunięcia ze względu na silne siły elektrostatyczne między nimi a powierzchnią płytki, co wymaga specjalnego traktowania.
Usuwanie substancji organicznych: Zanieczyszczenia organiczne, takie jak tłuszcz i pozostałości fotorezystu, mogą przylegać do powierzchni płytki. Zanieczyszczenia te są zazwyczaj usuwane za pomocą silnych środków utleniających lub rozpuszczalników.
Usuwanie jonów metali: Pozostałości jonów metali na powierzchni płytki półprzewodnikowej mogą pogorszyć parametry elektryczne, a nawet wpłynąć na późniejsze etapy przetwarzania. Dlatego do usuwania tych jonów stosuje się specjalne roztwory chemiczne.
Usuwanie tlenków: Niektóre procesy wymagają, aby powierzchnia płytki była wolna od warstw tlenków, takich jak tlenek krzemu. W takich przypadkach naturalne warstwy tlenków muszą zostać usunięte podczas określonych etapów czyszczenia.
Wyzwaniem w technologii czyszczenia płytek półprzewodnikowych jest skuteczne usuwanie zanieczyszczeń bez negatywnego wpływu na powierzchnię płytki, np. zapobieganie szorstkości powierzchni, korozji lub innym uszkodzeniom fizycznym.
2. Przebieg procesu czyszczenia płytek
Proces czyszczenia wafli zwykle obejmuje wiele etapów, które mają na celu zagwarantowanie całkowitego usunięcia zanieczyszczeń i uzyskanie całkowicie czystej powierzchni.
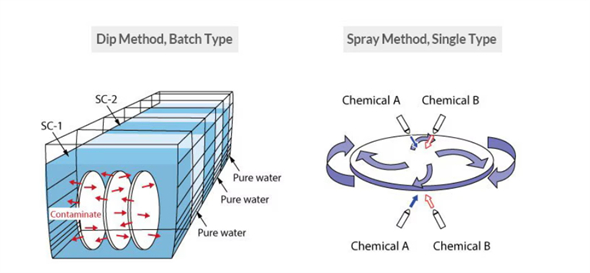
Rysunek: Porównanie czyszczenia wsadowego i czyszczenia pojedynczych płytek
Typowy proces czyszczenia płytek półprzewodnikowych obejmuje następujące główne kroki:
1. Czyszczenie wstępne (Pre-Clean)
Celem wstępnego czyszczenia jest usunięcie luźnych zanieczyszczeń i dużych cząstek z powierzchni płytki półprzewodnikowej, co zazwyczaj osiąga się poprzez płukanie wodą dejonizowaną (DI) i czyszczenie ultradźwiękowe. Woda dejonizowana może wstępnie usunąć cząstki i rozpuszczone zanieczyszczenia z powierzchni płytki półprzewodnikowej, natomiast czyszczenie ultradźwiękowe wykorzystuje zjawisko kawitacji, aby rozerwać wiązania między cząstkami a powierzchnią płytki, ułatwiając ich usunięcie.
2. Czyszczenie chemiczne
Czyszczenie chemiczne stanowi jeden z najważniejszych etapów procesu czyszczenia wafli. Polega na użyciu roztworów chemicznych w celu usunięcia z powierzchni wafla materiałów organicznych, jonów metali i tlenków.
Usuwanie substancji organicznych: Zazwyczaj do rozpuszczania i utleniania zanieczyszczeń organicznych stosuje się aceton lub mieszaninę amoniaku i nadtlenku (SC-1). Typowy stosunek dla roztworu SC-1 wynosi NH₄OH.
₂O₂
₂O = 1:1:5, przy temperaturze roboczej około 20°C.
Usuwanie jonów metali: Do usuwania jonów metali z powierzchni płytki stosuje się kwas azotowy lub mieszaninę kwasu solnego i nadtlenku (SC-2). Typowy stosunek roztworu SC-2 to HCl.
₂O₂
₂O = 1:1:6, przy czym temperatura utrzymywana jest na poziomie około 80°C.
Usuwanie tlenków: W niektórych procesach wymagane jest usunięcie rodzimej warstwy tlenków z powierzchni płytki, do czego stosuje się roztwór kwasu fluorowodorowego (HF). Typowy stosunek roztworu HF wynosi HF.
₂O = 1:50 i można go stosować w temperaturze pokojowej.
3. Czyszczenie końcowe
Po czyszczeniu chemicznym, wafle zazwyczaj przechodzą etap końcowego czyszczenia, aby upewnić się, że na powierzchni nie pozostały żadne pozostałości chemiczne. Czyszczenie końcowe odbywa się głównie przy użyciu wody dejonizowanej do dokładnego płukania. Dodatkowo, w celu usunięcia wszelkich pozostałych zanieczyszczeń z powierzchni wafli, stosuje się czyszczenie wodą ozonową (O₃/H₂O).
4. Suszenie
Wyczyszczone płytki muszą być szybko wysuszone, aby zapobiec powstawaniu zacieków i ponownemu osadzaniu się zanieczyszczeń. Typowe metody suszenia obejmują wirowanie i przedmuchiwanie azotem. Pierwsza metoda usuwa wilgoć z powierzchni płytki poprzez wirowanie z dużą prędkością, druga natomiast zapewnia całkowite wysuszenie poprzez nadmuch suchego azotu na powierzchnię płytki.
Zanieczyszczenie
Nazwa procedury czyszczenia
Opis mieszaniny chemicznej
Chemikalia
Cząsteczki | Pirania (SPM) | Kwas siarkowy/nadtlenek wodoru/woda dejonizowana | H2SO4/H2O2/H2O 3-4:1; 90°C |
SC-1 (APM) | Wodorotlenek amonu/nadtlenek wodoru/woda dejonizowana | NH4OH/H2O2/H2O 1:4:20; 80°C | |
Metale (nie miedź) | SC-2 (HPM) | Kwas solny/nadtlenek wodoru/woda dejonizowana | HCl/H2O2/H2O1:1:6; 85°C |
Pirania (SPM) | Kwas siarkowy/nadtlenek wodoru/woda dejonizowana | H2SO4/H2O2/H2O3-4:1; 90°C | |
DHF | Rozcieńczony kwas fluorowodorowy/woda dejonizowana (nie usuwa miedzi) | HF/H2O1:50 | |
Organiczne | Pirania (SPM) | Kwas siarkowy/nadtlenek wodoru/woda dejonizowana | H2SO4/H2O2/H2O 3-4:1; 90°C |
SC-1 (APM) | Wodorotlenek amonu/nadtlenek wodoru/woda dejonizowana | NH4OH/H2O2/H2O 1:4:20; 80°C | |
DIO3 | Ozon w wodzie dejonizowanej | Mieszaniny zoptymalizowane pod kątem O3/H2O | |
Tlenek rodzimy | DHF | Rozcieńczony kwas fluorowodorowy/woda dejonizowana | HF/H2O 1:100 |
BHF | Buforowany kwas fluorowodorowy | NH4F/HF/H2O |
3. Typowe metody czyszczenia płytek
1. Metoda czyszczenia RCA
Metoda czyszczenia RCA to jedna z najbardziej klasycznych technik czyszczenia płytek półprzewodnikowych w branży półprzewodników, opracowana przez firmę RCA Corporation ponad 40 lat temu. Metoda ta służy głównie do usuwania zanieczyszczeń organicznych i jonów metali i może być przeprowadzona w dwóch etapach: SC-1 (Standardowe Czyszczenie 1) i SC-2 (Standardowe Czyszczenie 2).
Czyszczenie SC-1: Ten etap służy głównie do usuwania zanieczyszczeń organicznych i cząstek. Roztwór jest mieszaniną amoniaku, nadtlenku wodoru i wody, która tworzy cienką warstwę tlenku krzemu na powierzchni płytki.
Czyszczenie SC-2: Ten etap służy przede wszystkim do usuwania zanieczyszczeń jonami metali za pomocą mieszaniny kwasu solnego, nadtlenku wodoru i wody. Pozostawia on cienką warstwę pasywacyjną na powierzchni płytki, zapobiegając ponownemu zanieczyszczeniu.
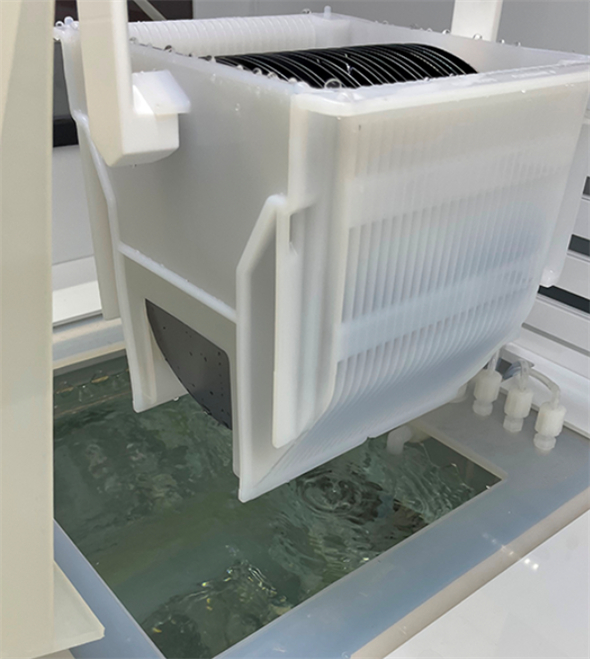
2. Metoda czyszczenia piranha (Piranha Etch Clean)
Metoda czyszczenia Piranha to wysoce skuteczna technika usuwania substancji organicznych, wykorzystująca mieszaninę kwasu siarkowego i nadtlenku wodoru, zazwyczaj w stosunku 3:1 lub 4:1. Ze względu na wyjątkowo silne właściwości utleniające tego roztworu, może on usuwać dużą ilość materii organicznej i uporczywych zanieczyszczeń. Metoda ta wymaga ścisłej kontroli warunków, szczególnie pod względem temperatury i stężenia, aby uniknąć uszkodzenia płytki.
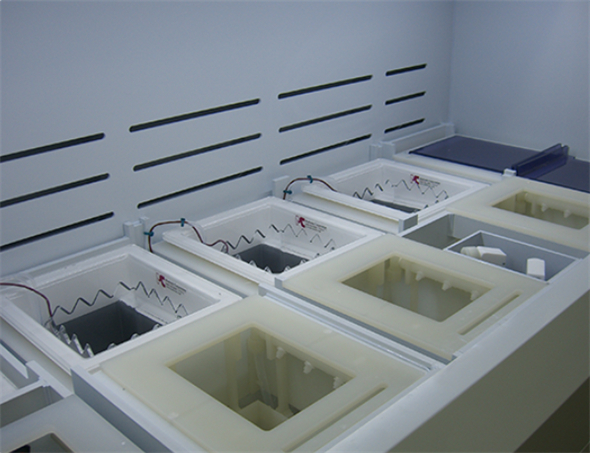
Czyszczenie ultradźwiękowe wykorzystuje efekt kawitacji generowany przez fale dźwiękowe o wysokiej częstotliwości w cieczy do usuwania zanieczyszczeń z powierzchni płytki. W porównaniu z tradycyjnym czyszczeniem ultradźwiękowym, czyszczenie megasoniczne działa z wyższą częstotliwością, umożliwiając skuteczniejsze usuwanie cząstek o rozmiarach submikronowych bez uszkadzania powierzchni płytki.
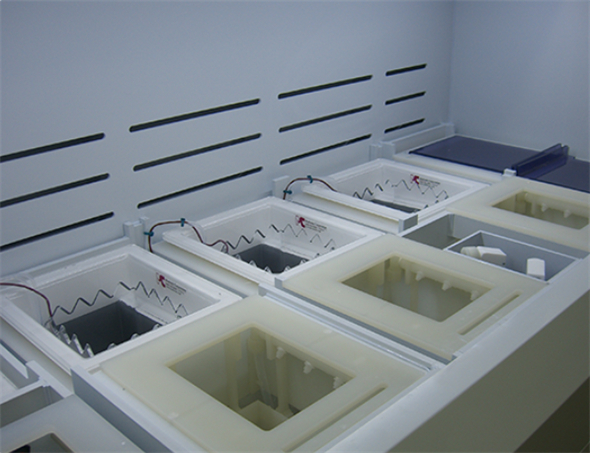
4. Czyszczenie ozonem
Technologia czyszczenia ozonem wykorzystuje silne właściwości utleniające ozonu do rozkładu i usuwania zanieczyszczeń organicznych z powierzchni wafli, ostatecznie przekształcając je w nieszkodliwy dwutlenek węgla i wodę. Metoda ta nie wymaga stosowania drogich odczynników chemicznych i powoduje mniejsze zanieczyszczenie środowiska, co czyni ją nową technologią w dziedzinie czyszczenia wafli.
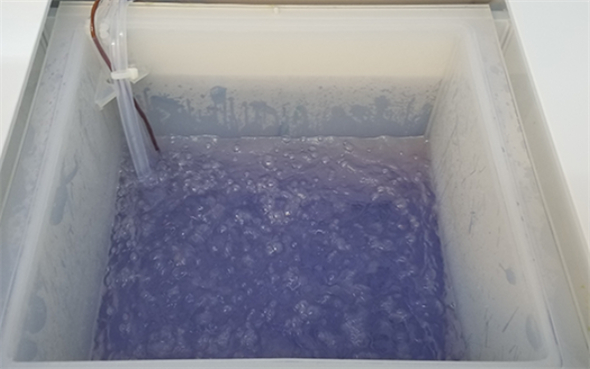
4. Sprzęt do czyszczenia płytek półprzewodnikowych
Aby zapewnić wydajność i bezpieczeństwo procesów czyszczenia płytek półprzewodnikowych, w produkcji półprzewodników stosuje się różnorodne, zaawansowane urządzenia czyszczące. Do głównych typów należą:
1. Sprzęt do czyszczenia na mokro
Sprzęt do czyszczenia na mokro obejmuje różnego rodzaju zbiorniki zanurzeniowe, zbiorniki do czyszczenia ultradźwiękowego oraz suszarki wirowe. Urządzenia te łączą siły mechaniczne z odczynnikami chemicznymi, aby usunąć zanieczyszczenia z powierzchni płytki. Zbiorniki zanurzeniowe są zazwyczaj wyposażone w systemy kontroli temperatury, aby zapewnić stabilność i skuteczność roztworów chemicznych.
2. Sprzęt do czyszczenia na sucho
Urządzenia do czyszczenia na sucho obejmują głównie urządzenia do czyszczenia plazmowego, które wykorzystują wysokoenergetyczne cząsteczki w plazmie do reakcji z powierzchnią płytki i usuwania z niej pozostałości. Czyszczenie plazmowe jest szczególnie odpowiednie w procesach wymagających zachowania integralności powierzchni bez wprowadzania pozostałości chemicznych.
3. Automatyczne systemy czyszczące
Wraz z ciągłym rozwojem produkcji półprzewodników, zautomatyzowane systemy czyszczące stały się preferowanym wyborem do czyszczenia płytek półprzewodnikowych na dużą skalę. Systemy te często obejmują automatyczne mechanizmy transferowe, wielozbiornikowe systemy czyszczące oraz precyzyjne systemy sterowania, aby zapewnić spójne rezultaty czyszczenia każdej płytki.
5. Trendy przyszłości
Wraz ze zmniejszaniem się liczby urządzeń półprzewodnikowych, technologia czyszczenia płytek półprzewodnikowych ewoluuje w kierunku bardziej wydajnych i przyjaznych dla środowiska rozwiązań. Przyszłe technologie czyszczenia będą koncentrować się na:
Usuwanie cząstek subnanometrowych: Obecne technologie czyszczenia umożliwiają usuwanie cząstek nanometrowych, jednak wraz z dalszym zmniejszaniem rozmiarów urządzeń usuwanie cząstek subnanometrowych stanie się nowym wyzwaniem.
Ekologiczne i przyjazne dla środowiska sprzątanie: Coraz ważniejsze będzie ograniczanie stosowania szkodliwych dla środowiska środków chemicznych i opracowywanie bardziej ekologicznych metod czyszczenia, takich jak czyszczenie ozonem i czyszczenie megadźwiękowe.
Wyższy poziom automatyzacji i inteligencji: Inteligentne systemy umożliwią monitorowanie w czasie rzeczywistym i dostosowywanie różnych parametrów podczas procesu czyszczenia, co jeszcze bardziej zwiększy skuteczność czyszczenia i wydajność produkcji.
Technologia czyszczenia płytek półprzewodnikowych, jako kluczowy etap w produkcji półprzewodników, odgrywa kluczową rolę w zapewnieniu czystości powierzchni płytek w kolejnych procesach. Połączenie różnych metod czyszczenia skutecznie usuwa zanieczyszczenia, zapewniając czystą powierzchnię podłoża w kolejnych etapach. Wraz z postępem technologii, procesy czyszczenia będą nadal optymalizowane, aby sprostać zapotrzebowaniu na wyższą precyzję i niższy wskaźnik defektów w produkcji półprzewodników.
Czas publikacji: 08-10-2024