SPC (Statistical Process Control) to kluczowe narzędzie w procesie produkcji płytek krzemowych, służące do monitorowania, kontrolowania i poprawy stabilności różnych etapów produkcji.
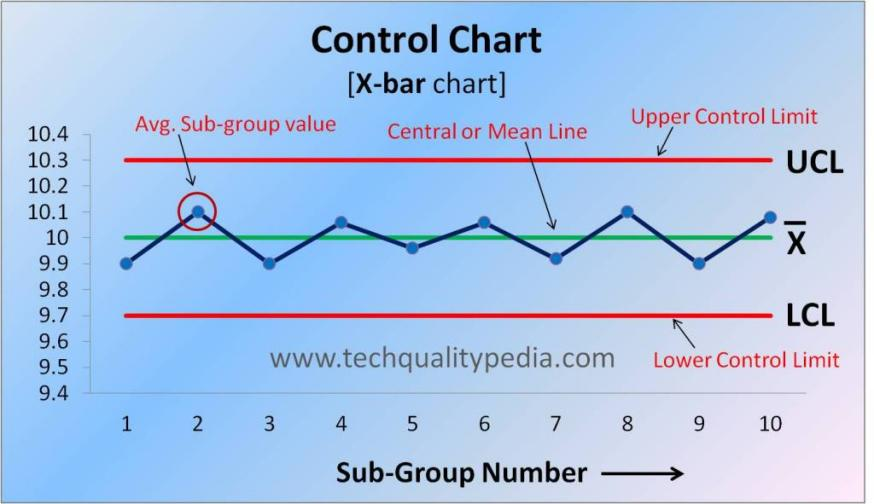
1. Przegląd systemu SPC
SPC to metoda wykorzystująca techniki statystyczne do monitorowania i kontrolowania procesów produkcyjnych. Jej podstawową funkcją jest wykrywanie anomalii w procesie produkcyjnym poprzez zbieranie i analizowanie danych w czasie rzeczywistym, co pomaga inżynierom dokonywać terminowych korekt i decyzji. Celem SPC jest zmniejszenie zmienności w procesie produkcyjnym, zapewniając, że jakość produktu pozostaje stabilna i spełnia specyfikacje.
SPC stosuje się w procesie trawienia w celu:
Monitoruj krytyczne parametry sprzętu (np. szybkość trawienia, moc RF, ciśnienie w komorze, temperaturę itp.)
Przeprowadź analizę kluczowych wskaźników jakości produktu (np. szerokość linii, głębokość trawienia, chropowatość krawędzi itp.)
Monitorując te parametry, inżynierowie mogą wykrywać trendy wskazujące na pogorszenie się wydajności sprzętu lub odchylenia w procesie produkcyjnym, zmniejszając w ten sposób liczbę wybrakowanych produktów.
2. Podstawowe komponenty systemu SPC
System SPC składa się z kilku kluczowych modułów:
Moduł gromadzenia danych: Zbiera dane w czasie rzeczywistym z urządzeń i przepływów procesowych (np. poprzez systemy FDC, EES) i rejestruje ważne parametry i wyniki produkcji.
Moduł wykresów kontrolnych: Wykorzystuje statystyczne wykresy kontrolne (np. wykres X-Bar, wykres R, wykres Cp/Cpk) w celu wizualizacji stabilności procesu i pomocy w ustaleniu, czy proces jest pod kontrolą.
System alarmowy: uruchamia alarmy, gdy krytyczne parametry przekroczą limity kontrolne lub pojawią się zmiany trendów, nakazując inżynierom podjęcie działań.
Moduł analizy i raportowania: analizuje przyczyny anomalii na podstawie wykresów SPC i regularnie generuje raporty dotyczące wydajności procesu i urządzeń.
3. Szczegółowe wyjaśnienie kart kontrolnych w SPC
Wykresy kontrolne są jednym z najczęściej używanych narzędzi w SPC, pomagającym odróżnić „normalne odchylenia” (spowodowane naturalnymi odchyleniami procesu) od „odchyleń nienormalnych” (spowodowanych awariami sprzętu lub odchyleniami procesu). Typowe wykresy kontrolne obejmują:
Wykresy X-Bar i R: służą do monitorowania średniej i zakresu w obrębie partii produkcyjnych w celu sprawdzenia, czy proces jest stabilny.
Wskaźniki Cp i Cpk: służą do pomiaru zdolności procesu, tj. czy wynik procesu może stale spełniać wymagania specyfikacji. Cp mierzy potencjalną zdolność, podczas gdy Cpk bierze pod uwagę odchylenie centrum procesu od limitów specyfikacji.
Na przykład w procesie trawienia możesz monitorować parametry, takie jak szybkość trawienia i chropowatość powierzchni. Jeśli szybkość trawienia określonego elementu wyposażenia przekracza limit kontrolny, możesz użyć wykresów kontrolnych, aby ustalić, czy jest to naturalna zmiana, czy też oznaka awarii wyposażenia.
4. Zastosowanie SPC w urządzeniach trawiących
W procesie trawienia kontrola parametrów sprzętu ma kluczowe znaczenie, a technologia SPC pomaga poprawić stabilność procesu w następujący sposób:
Monitorowanie stanu sprzętu: Systemy takie jak FDC zbierają dane w czasie rzeczywistym na temat kluczowych parametrów sprzętu do trawienia (np. moc RF, przepływ gazu) i łączą te dane z wykresami kontrolnymi SPC w celu wykrycia potencjalnych problemów ze sprzętem. Na przykład, jeśli zauważysz, że moc RF na wykresie kontrolnym stopniowo odbiega od ustawionej wartości, możesz podjąć wczesne działania w celu regulacji lub konserwacji, aby uniknąć wpływu na jakość produktu.
Monitorowanie jakości produktu: Możesz również wprowadzić kluczowe parametry jakości produktu (np. głębokość trawienia, szerokość linii) do systemu SPC, aby monitorować ich stabilność. Jeśli niektóre krytyczne wskaźniki produktu stopniowo odbiegają od wartości docelowych, system SPC wygeneruje alarm, wskazując, że konieczne są zmiany w procesie.
Konserwacja zapobiegawcza (PM): SPC może pomóc zoptymalizować cykl konserwacji zapobiegawczej sprzętu. Analizując długoterminowe dane dotyczące wydajności sprzętu i wyników procesów, możesz określić optymalny czas konserwacji sprzętu. Na przykład, monitorując moc RF i żywotność ESC, możesz określić, kiedy konieczne jest czyszczenie lub wymiana podzespołów, zmniejszając liczbę awarii sprzętu i przestojów w produkcji.
5. Wskazówki dotyczące codziennego użytkowania systemu SPC
Podczas codziennego stosowania systemu SPC należy postępować zgodnie z poniższymi krokami:
Zdefiniuj kluczowe parametry kontrolne (KPI): Zidentyfikuj najważniejsze parametry w procesie produkcyjnym i uwzględnij je w monitorowaniu SPC. Parametry te powinny być ściśle powiązane z jakością produktu i wydajnością sprzętu.
Ustaw limity kontrolne i limity alarmowe: Na podstawie danych historycznych i wymagań procesu ustaw rozsądne limity kontrolne i limity alarmowe dla każdego parametru. Limity kontrolne są zwykle ustawiane na ±3σ (odchylenia standardowe), podczas gdy limity alarmowe są oparte na konkretnych warunkach procesu i sprzętu.
Ciągły monitoring i analiza: Regularnie przeglądaj wykresy kontrolne SPC, aby analizować trendy i odchylenia danych. Jeśli niektóre parametry przekraczają limity kontrolne, konieczne jest natychmiastowe działanie, takie jak dostosowanie parametrów sprzętu lub przeprowadzenie konserwacji sprzętu.
Obsługa nieprawidłowości i analiza przyczyn źródłowych: Gdy wystąpi nieprawidłowość, system SPC rejestruje szczegółowe informacje o incydencie. Musisz rozwiązać problemy i przeanalizować przyczynę źródłową nieprawidłowości na podstawie tych informacji. Często możliwe jest połączenie danych z systemów FDC, systemów EES itp., aby przeanalizować, czy problem jest spowodowany awarią sprzętu, odchyleniem procesu lub zewnętrznymi czynnikami środowiskowymi.
Ciągłe doskonalenie: Korzystając z danych historycznych zarejestrowanych przez system SPC, zidentyfikuj słabe punkty w procesie i zaproponuj plany ulepszeń. Na przykład w procesie trawienia przeanalizuj wpływ żywotności ESC i metod czyszczenia na cykle konserwacji sprzętu i stale optymalizuj parametry operacyjne sprzętu.
6. Przypadek zastosowania praktycznego
Jako praktyczny przykład, załóżmy, że jesteś odpowiedzialny za sprzęt do trawienia E-MAX, a katoda komory ulega przedwczesnemu zużyciu, co prowadzi do wzrostu wartości D0 (wada BARC). Monitorując moc RF i szybkość trawienia za pomocą systemu SPC, zauważasz trend, w którym te parametry stopniowo odbiegają od swoich ustawionych wartości. Po wyzwoleniu alarmu SPC łączysz dane z systemu FDC i ustalasz, że problem jest spowodowany niestabilną kontrolą temperatury wewnątrz komory. Następnie wdrażasz nowe metody czyszczenia i strategie konserwacji, ostatecznie zmniejszając wartość D0 z 4,3 do 2,4, co poprawia jakość produktu.
7. W XINKEHUI możesz otrzymać.
W XINKEHUI możesz uzyskać idealny wafel, niezależnie od tego, czy jest to wafel krzemowy, czy wafel SiC. Specjalizujemy się w dostarczaniu najwyższej jakości wafli dla różnych branż, skupiając się na precyzji i wydajności.
(płytka krzemowa)
Nasze płytki krzemowe charakteryzują się najwyższą czystością i jednorodnością, co gwarantuje znakomite właściwości elektryczne dla Twoich potrzeb w zakresie półprzewodników.
W przypadku bardziej wymagających zastosowań nasze wafle SiC zapewniają wyjątkową przewodność cieplną i wyższą wydajność energetyczną, co czyni je idealnymi do układów elektroniki dużej mocy i środowisk o wysokiej temperaturze.
(płytka SiC)
Dzięki XINKEHUI otrzymujesz najnowocześniejszą technologię i niezawodne wsparcie, gwarantujące wafle spełniające najwyższe standardy branżowe. Wybierz nas, aby uzyskać doskonałość wafli!
Czas publikacji: 16-10-2024